Swing bolster load test structure and method
A technology of load testing and bolster, applied in the direction of measuring force, measuring device, instrument, etc., can solve the problems affecting the fatigue reliability research of truck structure, inaccurate load spectrum of truck, inaccurate test structure, etc., and shorten the test work. The effect of reducing the number of cycles, reducing the steps of load calibration, and reducing the workload of the later stage
- Summary
- Abstract
- Description
- Claims
- Application Information
AI Technical Summary
Problems solved by technology
Method used
Image
Examples
Embodiment Construction
[0046] Such as figure 2 Shown is the bolster load test structure adopted by the present invention. The bolster 10' includes a center plate 11 and side bearings 12 arranged on both sides of the center plate 11. The improvements include:
[0047]A center disc dynamometer 20 is processed at the center disc 11, and the center disc dynamometer 20 is a circular blind hole for a center disc load cell assembly 30 to be placed therein. On the side of the center disc dynamometer 20 There is a raised edge 201 to replace the lower center plate on the bolster 10'; when the center plate 11 of the bolster 10' is installed on the bogie, first the center plate load cell assembly 30 Place it on the bottom of the center disc dynamometer 20, then make the lower center disc of the car body fall into the raised edge 201, and press it above the center disc load cell assembly 30, and then use a pin The shaft passes through the lower center plate, the center plate load cell assembly 30 and the centr...
PUM
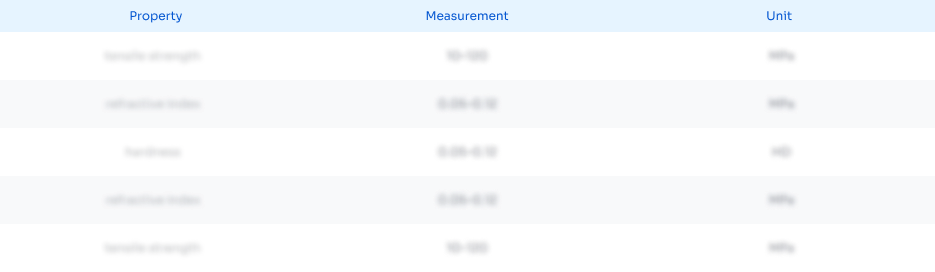
Abstract
Description
Claims
Application Information

- Generate Ideas
- Intellectual Property
- Life Sciences
- Materials
- Tech Scout
- Unparalleled Data Quality
- Higher Quality Content
- 60% Fewer Hallucinations
Browse by: Latest US Patents, China's latest patents, Technical Efficacy Thesaurus, Application Domain, Technology Topic, Popular Technical Reports.
© 2025 PatSnap. All rights reserved.Legal|Privacy policy|Modern Slavery Act Transparency Statement|Sitemap|About US| Contact US: help@patsnap.com