Minitype paster fuse and method of manufacturing the same
A fuse and patch technology, applied in fuse manufacturing, emergency protection devices, electrical components, etc., can solve problems affecting resistance, electrical performance consistency, penetration, etc., and achieve the effect of inhibiting penetration and thermal insulation penetration.
- Summary
- Abstract
- Description
- Claims
- Application Information
AI Technical Summary
Problems solved by technology
Method used
Image
Examples
Embodiment 1
[0024] see figure 1 It is the top view structure schematic diagram of the raw film of the present invention and figure 2 It is a schematic diagram of the side section structure of the small patch fuse of the present invention.
[0025] A small chip fuse 102, with a glass ceramic layer 100 as a substrate, and the material of the glass ceramic layer 100 is one of alumina, titanium dioxide, calcium aluminosilicate, alumina, borosilicate glass, calcium borosilicate or A variety of mixtures; use the fuse metal or alloy as the internal electrode 103 to form a monolithic structure, and the material of the internal electrode 103 is a metal or an alloy of multiple metals among gold, silver, copper, aluminum, palladium, and platinum; monolithic Both ends of the structure are provided with terminal electrodes 105,106.
[0026] A layer of internal electrodes 103 is arranged between the two layers of glass ceramic layers 100. The two ends of the internal electrodes 103 are in contact wi...
Embodiment 2
[0030] see image 3 As shown in the schematic diagram of the side sectional structure of the small chip fuse according to Embodiment 2 of the present invention, a small chip fuse 102' is based on a glass ceramic layer 100, and the material of the glass ceramic layer 100 is alumina, titanium dioxide, aluminosilicate A mixture of one or more of calcium salt, alumina, borosilicate glass, and calcium borosilicate; a monolithic structure is formed with a fuse metal or alloy as the internal electrode 103, and the material of the internal electrode 103 is gold, silver, or copper , aluminum, palladium, platinum or a metal alloy; the two ends of the monolithic structure are provided with terminal electrodes 105,106.
[0031] Two layers of internal electrodes 103 are arranged between the three layers of glass ceramic layers 100. Both ends of the two layers of internal electrodes 103 are in contact with terminal electrodes 105 and 106 respectively. The middle part of the internal electro...
PUM
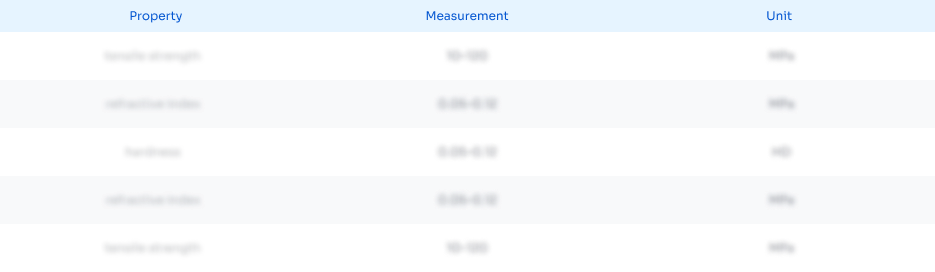
Abstract
Description
Claims
Application Information

- R&D
- Intellectual Property
- Life Sciences
- Materials
- Tech Scout
- Unparalleled Data Quality
- Higher Quality Content
- 60% Fewer Hallucinations
Browse by: Latest US Patents, China's latest patents, Technical Efficacy Thesaurus, Application Domain, Technology Topic, Popular Technical Reports.
© 2025 PatSnap. All rights reserved.Legal|Privacy policy|Modern Slavery Act Transparency Statement|Sitemap|About US| Contact US: help@patsnap.com