Method and special equipment for recycling to produce fuel
A technology of organic waste and special equipment, used in special forms of dry distillation, petroleum industry, coke ovens, etc., can solve the problems of non-continuous normal operation, cumbersome process and equipment, uneven heating of organic waste, etc. The effect of small internal volume and reduced replacement frequency
- Summary
- Abstract
- Description
- Claims
- Application Information
AI Technical Summary
Problems solved by technology
Method used
Image
Examples
Embodiment Construction
[0019] See figure 1 , Separate the domestic garbage to remove metal and inorganic matter, separate the organic garbage, and pass the organic garbage from the feed hopper 1 through the conveying tubes 3-3 on both sides of the tubular cracking furnace 3 to the furnace to the collector 3-6 In the middle push, the advancing speed is 60~65 rpm, heating and depolymerizing at the temperature of 220~240℃, the spiral hinge rod is installed in the conveying tube 3-3, and the material is expanded to the middle of the cracking furnace controlled by the speed regulating motor 2. The radial concentrators 3-6 are advanced, and the electric heating device 12 respectively heats up and heats the conveying tube, the cracking furnace concentrator and the concentrating pipeline between the primary slag discharger.
[0020] The gas material depolymerized by the cracking furnace first enters the gas buffer 4, and the inner wall of the buffer 4 is provided with staggered baffles. The gas flow direction ...
PUM
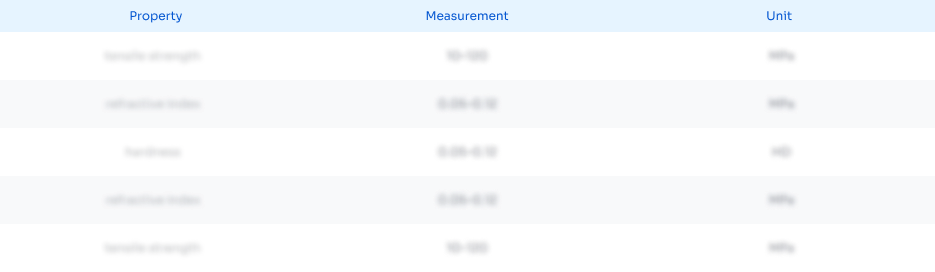
Abstract
Description
Claims
Application Information

- R&D
- Intellectual Property
- Life Sciences
- Materials
- Tech Scout
- Unparalleled Data Quality
- Higher Quality Content
- 60% Fewer Hallucinations
Browse by: Latest US Patents, China's latest patents, Technical Efficacy Thesaurus, Application Domain, Technology Topic, Popular Technical Reports.
© 2025 PatSnap. All rights reserved.Legal|Privacy policy|Modern Slavery Act Transparency Statement|Sitemap|About US| Contact US: help@patsnap.com