Printing device and printing method for integrating electronic components
A technology for electronic components and printing devices, applied in electrical components, printing devices, printing and other directions, can solve the problems of unfavorable wiring modification, waste of resources, complicated processing technology, etc., and achieve the effect of good processing flexibility, easy operation and simple process
- Summary
- Abstract
- Description
- Claims
- Application Information
AI Technical Summary
Problems solved by technology
Method used
Image
Examples
no. 1 example
[0053] This solution prints fine interconnected metal wires by direct printing of metal ink, and uses fine interconnected metal wires to electrically connect the 3*4 CMOS active pixel image sensor module arrays on the substrate to form a complete flat panel detection device. The substrate composed of multiple CMOS active pixel image sensor modules is not flat, each CMOS active pixel image sensor and solder joints are higher than the surface of the substrate, and there is a gap between the image sensor and the image sensor, so that There will be a groove (that is, the modules on the entire substrate form a step), and the existing inkjet printing device that can only print patterns on a flat surface can no longer meet the requirements, so a design suitable for this program is designed. Printing device and printing method.
[0054] First, the inkjet printing printing device is designed in a clean cabinet to ensure that the surface of the module to be printed is clean so that the...
no. 2 example
[0101] In this embodiment, the pattern of fine interconnected metal wires is printed by direct printing of metal ink, and a plurality of pre-encapsulated IC chip modules or encapsulated chips on the substrate are electrically connected to each other with fine interconnected metal wires to replace The traditional metal wire connection and PCB copper cladding process greatly reduce the cost of processing and increase the flexibility of interconnection.
[0102] also adopted figure 1 The printing device of inkjet printing is an application example of making interconnection wires on a substrate fixed with multiple electronic components, and connecting independent units into a complete electronic device. Since the solder joints of the electronic chips on the substrate will be on the On the surface, the wiring path printed in this way will pass through the vertical surface of the steps. In order to print high-quality metal wires under such circumstances, a high-precision platform is...
PUM
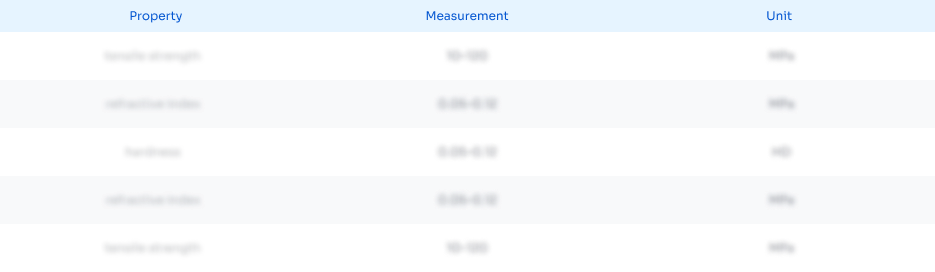
Abstract
Description
Claims
Application Information

- Generate Ideas
- Intellectual Property
- Life Sciences
- Materials
- Tech Scout
- Unparalleled Data Quality
- Higher Quality Content
- 60% Fewer Hallucinations
Browse by: Latest US Patents, China's latest patents, Technical Efficacy Thesaurus, Application Domain, Technology Topic, Popular Technical Reports.
© 2025 PatSnap. All rights reserved.Legal|Privacy policy|Modern Slavery Act Transparency Statement|Sitemap|About US| Contact US: help@patsnap.com