Hot forging composite die manufacturing method and hot forging composite die
A composite mold and manufacturing method technology, applied in manufacturing tools, forging/pressing/hammering machinery, forging/pressing/hammer devices, etc., can solve the problems of long mold development cycle, high manufacturing cost, low bearing capacity, etc. The effect of shortening the development cycle, long service life and strong bearing capacity
- Summary
- Abstract
- Description
- Claims
- Application Information
AI Technical Summary
Problems solved by technology
Method used
Image
Examples
Embodiment 1
[0032] Such as figure 1 , figure 2 and image 3 As shown, the hot forging composite die includes an inner mold body 1 and an outer mold body 2 . The inner mold body 1 is block-shaped, and the inner mold body 1 is an integral cylinder. A concave mold cavity 11 is opened on the inner mold body 1 . The shape of the mold cavity 11 here can be designed as required. The outer mold body 2 is an integral structure, and the outer mold body 2 is provided with a concave inner mold mounting seat 21. The shape of the above-mentioned inner mold body 1 matches the shape of the inner mold mounting seat 21, and when the inner mold body 1 is installed When entering the inner mold mounting seat 21, the mold cavity 11 faces the outside of the inner mold mounting seat 21.
[0033] The bottom of the outer mold body 2 is provided with an exhaust hole 22 communicating with the inner mold mounting seat 21 . The outer wall of the inner mold body 1 is in sealing fit with the inner wall of the inn...
Embodiment 2
[0047] Such as Figure 4 , Figure 5 and Figure 6 As shown, in this embodiment, the shape of the inner mold body 1 is an elliptical cylinder, and the shape of the inner mold body 1 matches the shape of the inner mold mounting seat 21 . The rest are the same as in Example 1, and will not be repeated herein.
PUM
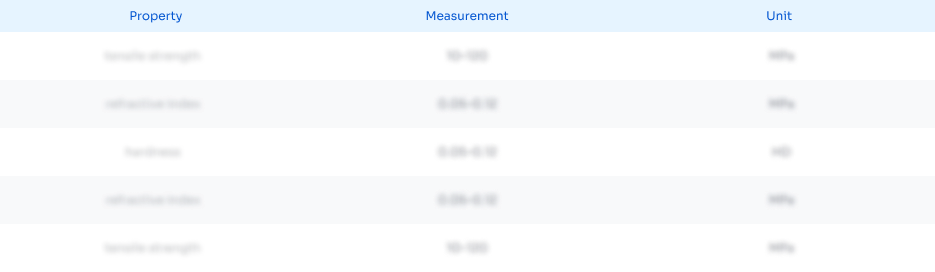
Abstract
Description
Claims
Application Information

- Generate Ideas
- Intellectual Property
- Life Sciences
- Materials
- Tech Scout
- Unparalleled Data Quality
- Higher Quality Content
- 60% Fewer Hallucinations
Browse by: Latest US Patents, China's latest patents, Technical Efficacy Thesaurus, Application Domain, Technology Topic, Popular Technical Reports.
© 2025 PatSnap. All rights reserved.Legal|Privacy policy|Modern Slavery Act Transparency Statement|Sitemap|About US| Contact US: help@patsnap.com