In-situ gas-phase method for preparing industrial zeolite catalyst
A zeolite catalyst, in-situ preparation technology, applied in molecular sieve catalysts, physical/chemical process catalysts, crystalline aluminosilicate zeolites, etc., can solve the problems of fine control of zeolite structure, difficult adjustment of film thickness and position, and adhesion strength Poor problems, to achieve the effect of improving utilization rate and catalytic performance, high utilization rate and low production cost
- Summary
- Abstract
- Description
- Claims
- Application Information
AI Technical Summary
Problems solved by technology
Method used
Image
Examples
Embodiment 1
[0022] 36 grams of silica sol, 2.62 grams of SB powder, 2.4 grams of sodium hydroxide and 1.08 grams of MCM-22 seed crystals are fully mixed, and the material ratio (molar ratio) of the reactants is: SiO 2 :Al 2 o 3 :Na + :=1:0.033:0.1. After thorough mixing, 3.6 grams of nitric acid and 50 grams of deionized water were added to the mixture to obtain silica-alumina gel, which was then extruded into strips with silica-alumina gel and dried. Take 1 gram of formed silica-alumina glue rod-shaped particles and put them on the bracket in a stainless steel reaction kettle lined with polytetrafluoroethylene. There are 3 grams of HMI and 4 grams of deionized water in the kettle, seal it, and crystallize in situ at 150 ° C. 8 days. Take out, wash, filter, dry at 120°C, and roast at 540°C for 10 hours to obtain the product. The obtained zeolite catalyst was determined by XRD and SEM to be MCM-22 zeolite catalyst, and the lateral pressure strength was 96N / CM.
Embodiment 2
[0024] 36 grams of silica sol, 2.62 grams of SB powder, 1.2 grams of sodium hydroxide and 1.08 grams of MCM-22 seed crystals are fully mixed evenly, and the material ratio (molar ratio) of the reactants is: SiO 2 :Al 2 o 3 :Na + :=1:0.033:0.05. After thorough mixing, 3.6 grams of nitric acid and 50 grams of deionized water were added to the mixture to obtain silica-alumina gel, which was then extruded into strips with silica-alumina gel and dried. Take 1 gram of formed silica-alumina glue rod-shaped particles and put them on the bracket in a stainless steel reaction kettle lined with polytetrafluoroethylene. There are 3 grams of HMI and 4 grams of deionized water in the kettle, seal it, and crystallize in situ at 150 ° C. 10 days. Take out, wash, filter, dry at 120°C, and roast at 540°C for 10 hours to obtain the product. The obtained zeolite catalyst was determined by XRD and SEM to be MCM-22 zeolite catalyst, and the lateral pressure strength was 102 N / CM.
Embodiment 3
[0026] 30 grams of silica sol, 2.62 grams of SB powder, 2 grams of sodium hydroxide and 0.9 grams of MCM-22 seed crystals are fully mixed evenly, and the material ratio (molar ratio) of the reactants is: SiO 2 :Al 2 o 3 :Na +:=1:0.04:0.1. After thorough mixing, 3 g of nitric acid and 40 g of deionized water were added to the mixture to obtain silica-alumina gel, and then the silica-alumina gel was extruded into strips and dried. Take 1 gram of formed silica-alumina glue rod-shaped particles and put them on the bracket in a stainless steel reaction kettle lined with polytetrafluoroethylene. There are 3 grams of HMI and 4 grams of deionized water in the kettle, seal it, and crystallize in situ at 150 ° C. 10 days. Take out, wash, filter, dry at 120°C, and roast at 540°C for 10 hours to obtain the product. XRD and SEM determined that the obtained zeolite catalyst was MCM-22 zeolite catalyst, and the lateral pressure strength was 80N / CM.
PUM
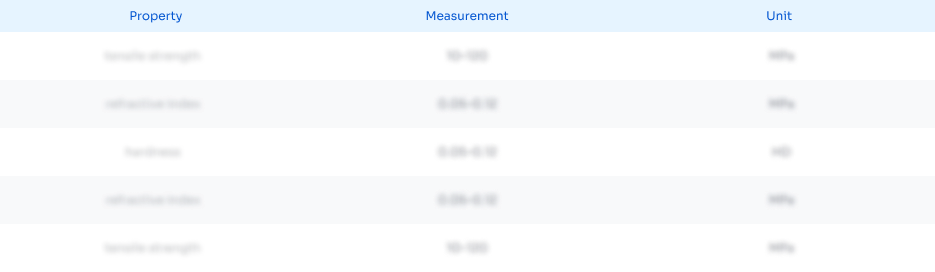
Abstract
Description
Claims
Application Information

- Generate Ideas
- Intellectual Property
- Life Sciences
- Materials
- Tech Scout
- Unparalleled Data Quality
- Higher Quality Content
- 60% Fewer Hallucinations
Browse by: Latest US Patents, China's latest patents, Technical Efficacy Thesaurus, Application Domain, Technology Topic, Popular Technical Reports.
© 2025 PatSnap. All rights reserved.Legal|Privacy policy|Modern Slavery Act Transparency Statement|Sitemap|About US| Contact US: help@patsnap.com