Low-temperature curing ceramic powder and method for producing the same
A technology of ceramic powder and low temperature, applied in the field of materials, can solve the problems of high scrap rate, high comprehensive performance, incomplete filling, etc., achieve stable material performance, excellent comprehensive effect, and solve the effect of easy flow
- Summary
- Abstract
- Description
- Claims
- Application Information
AI Technical Summary
Problems solved by technology
Method used
Image
Examples
Embodiment 1
[0025] Will Al 2 o 3 , SiO 2 and MgO were put into the high-temperature test kiln furnace for high-temperature pre-burning. The pre-burning method is: the Al 2 o 3 , SiO 2 Or MgO is heated to 1560°C to complete high-temperature pre-burning. The pre-burning temperature-time curve is as figure 1 shown.
[0026] Al 2 o 3 , SiO 2 and MgO were respectively put into a test ball mill, and water was added to impregnate the material until the water surface was 10 mm above the material; then ball milled to a fineness of 250-300 mesh. Al after ball milling 2 o 3 , SiO 2 , MgO is dried in a drying oven to remove moisture, the drying temperature is 120±5°C, and the drying time is 2h.
[0027] The thermosetting plastic PA6 and thermosetting plastic PC are pre-fired at low temperature. The pre-firing method is: heating to 120 °C at a heating rate of 7-8 °C / h, and then heating to 300 °C at a heating rate of 18-20 °C / h , to complete low temperature pre-firing. The pre-burning te...
Embodiment 2
[0032] Will Al 2 o 3 , SiO 2 and MgO were placed in the high-temperature test kiln furnace for high-temperature pre-burning. The pre-burning method is: the Al 2 o 3 , SiO 2 Or MgO is heated to 1500°C to complete high-temperature pre-burning. Al 2 o 3 , SiO 2 and MgO were respectively put into the test ball mill, and water was added to impregnate the material until the water surface was 12mm above the material; then ball milled to a fineness of 250-300 mesh. Al after ball milling 2 o 3 , SiO 2 , MgO is dried in a drying oven to remove moisture, the drying temperature is 120±5°C, and the drying time is 2h.
[0033] The thermosetting plastic PA66 and thermosetting plastic PC are pre-fired at low temperature. The pre-firing method is: heating to 120 °C at a heating rate of 7-8 °C / h, and then heating to 300 °C at a heating rate of 18-20 °C / h , to complete low temperature pre-firing.
[0034] Heat the thermosetting plastic PA66 and thermosetting plastic PC after low-tempe...
Embodiment 3
[0038] Will Al 2 o 3 , SiO 2 and MgO were put into the high-temperature test kiln furnace for high-temperature pre-burning. The pre-burning method is: the Al 2 o 3 , SiO 2 Or MgO is heated to 1575°C to complete high-temperature pre-burning. Al 2 o 3 , SiO 2 and MgO were respectively put into the test ball mill, and water was added to impregnate the material until the water surface was 13 mm above the material; then ball milled to a fineness of 250-300 mesh. Al after ball milling 2 o 3 , SiO 2 , MgO is dried in a drying oven to remove moisture, the drying temperature is 120±5°C, and the drying time is 2h.
[0039] The thermosetting plastic PA6 and thermosetting plastic PC are pre-fired at low temperature. The pre-firing method is: heating to 120 °C at a heating rate of 7-8 °C / h, and then heating to 300 °C at a heating rate of 18-20 °C / h , to complete low temperature pre-firing.
[0040] Heat the thermosetting plastic PA6 and thermosetting plastic PC after low-tempe...
PUM
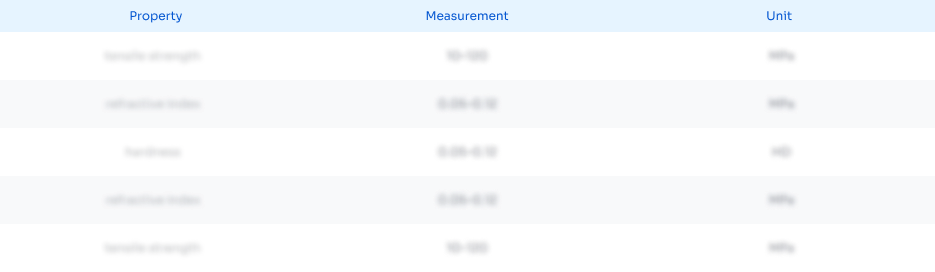
Abstract
Description
Claims
Application Information

- R&D
- Intellectual Property
- Life Sciences
- Materials
- Tech Scout
- Unparalleled Data Quality
- Higher Quality Content
- 60% Fewer Hallucinations
Browse by: Latest US Patents, China's latest patents, Technical Efficacy Thesaurus, Application Domain, Technology Topic, Popular Technical Reports.
© 2025 PatSnap. All rights reserved.Legal|Privacy policy|Modern Slavery Act Transparency Statement|Sitemap|About US| Contact US: help@patsnap.com