Method of manufacturing high-strength hot rolled ribbed steel bar
A technology of hot-rolled ribbed steel bar and ribbed steel bar, which is applied in metal rolling, temperature control, metal rolling and other directions, can solve the problems of increased consumption of vanadium-nitrogen alloy, insufficient production power, and inability to scale output, etc. The effect of reducing the amount of microalloys added, stable mechanical properties of the process, and economical society
- Summary
- Abstract
- Description
- Claims
- Application Information
AI Technical Summary
Problems solved by technology
Method used
Examples
Embodiment 1
[0022] A. Steel slabs with the following chemical composition: C 0.18%, Si 0.46%, Mn 1.22%, V 0.033%, S 0.021%, P 0.027%, and the rest is Fe and unavoidable impurities;
[0023] B. Put the billet above into a heating furnace with a furnace temperature of 1160°C. When heated to a billet temperature of 1010°C, send it to a rolling mill for rolling. During rolling, rough rolling is carried out for 65 seconds at a rolling speed of 1m / s. Afterwards, under the rolling condition of 4m / s, the middle rolling was carried out for 60 seconds at a speed, and at last, the finishing rolling was carried out for 75 seconds under the rolling condition of 16m / s;
[0024] C, the finishing rolled steel product of B step is 360m in cooling water 3 / h, under the condition of cooling water pressure of 1.4MPa, rapid cooling for 3 seconds to obtain steel with a temperature of 880°C, and then placed in the air to naturally cool to 250°C, that is, to obtain HRB500 fine-grained high-strength steel bars wi...
Embodiment 2
[0026] A. Steel slabs with the following chemical compositions: C 0.24%, Si 0.56%, Mn 1.51%, V 0.031%, S 0.016%, P 0.023%, and the rest are Fe and unavoidable impurities;
[0027] B. Send the above billet into a heating furnace with a furnace temperature of 1200°C. When the billet is heated to a temperature of 1050°C, it is sent to a rolling mill for rolling. During rolling, rough rolling is carried out for 60 seconds at a rolling speed of 1m / s. , followed by rolling for 60 seconds at a speed of 4m / s, and finishing rolling for 72 seconds at a speed of 7.8m / s;
[0028] C, the finish-rolled steel product of B step is 370m in cooling water total water 3 / h, under the condition of cooling water pressure of 1.9MPa, rapid cooling for 2 seconds to obtain steel with a temperature of 870°C, which is naturally air-cooled to 270°C on the upper cooling bed, collected and bundled, and the HRB500 fine-grained steel with a specification of Φ32mm is obtained. Strength steel bars.
[0029] T...
PUM
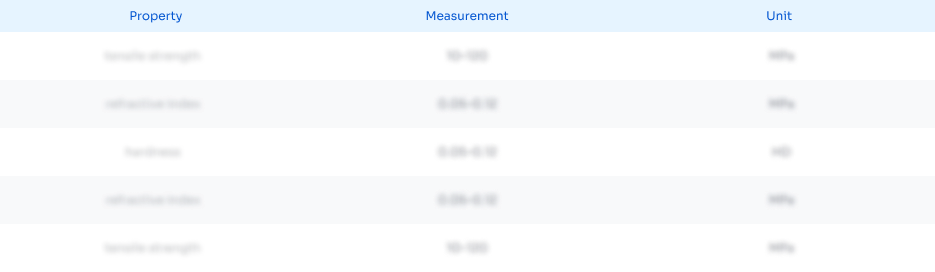
Abstract
Description
Claims
Application Information

- R&D
- Intellectual Property
- Life Sciences
- Materials
- Tech Scout
- Unparalleled Data Quality
- Higher Quality Content
- 60% Fewer Hallucinations
Browse by: Latest US Patents, China's latest patents, Technical Efficacy Thesaurus, Application Domain, Technology Topic, Popular Technical Reports.
© 2025 PatSnap. All rights reserved.Legal|Privacy policy|Modern Slavery Act Transparency Statement|Sitemap|About US| Contact US: help@patsnap.com