Optical fiber F-P acceleration and pressure sensor and its manufacturing method
A technology of pressure sensor and manufacturing method, applied in the direction of acceleration measurement using inertial force, fluid pressure measurement using optical method, cladding optical fiber, etc., can solve the problem of high temperature sensitivity, unfavorable large-scale manufacturing, and poor repeatability and other issues to achieve the effect of good optical performance
- Summary
- Abstract
- Description
- Claims
- Application Information
AI Technical Summary
Problems solved by technology
Method used
Image
Examples
Embodiment 1
[0029] Step 1, processing a deep 100 micron microgroove 4 with a 157nm ultraviolet laser on the quartz optical fiber 1, such as figure 1 shown;
[0030] Step 2, processing the end face of the connected optical fiber 2 with a 157nm ultraviolet laser to process a protrusion 3 with a length of 60 microns, such as figure 2 shown;
[0031] Step 3. Weld the optical fibers formed in step 1 and step 2 together to form a enamel cavity 5, wherein the end of the connected optical fiber 2 with the protrusion 3 is welded with the end of the optical fiber 1 with the microgroove 4, as shown in Figure 3 ;
[0032] Step 4, cutting the outer end face of the connected optical fiber 2 to form a diaphragm 6, that is, to make the optical fiber Fabac acceleration and pressure sensor with a hard center of mass (protrusion 3) of the present invention, as shown in Figure 4, the sensor's Spectral graph such as Figure 7 shown.
[0033] When in use, when the sensor feels pressure and acceleration, ...
Embodiment 2
[0035] Step 1, processing a microgroove 4 with a depth of 40 microns on the gem fiber 1 with a femtosecond laser;
[0036] Step 2. Weld together with the connected optical fiber 2 to form a Fappaure cavity 5, process a protrusion 3 with laser at the other end of the connected optical fiber 2, and form a diaphragm 6, thus forming a hard mass center (i.e. protrusion 3) Acceleration and pressure sensors, as shown in Figure 5.
Embodiment 3
[0038] Step 1, processing a microgroove 4 with a depth of 100 microns on the optical fiber 1;
[0039] Step 2, processing the end face of the connected optical fiber 2 with a 157nm ultraviolet laser to process a protrusion 3 with a length of 60 microns;
[0040] Step 3, welding the optical fibers formed in step 1 and step 2 together to form a enamel cavity 5, wherein one end of the connected optical fiber 2 having a protrusion 3 is welded to an end of the optical fiber 1 having a microgroove 4;
[0041] Step 4, process a protrusion 3 at the other end of the connected optical fiber 2, and form a diaphragm 6, thus forming an acceleration and pressure sensor with a hard center of mass, as shown in Figure 6, such a sensor has higher sensitivity.
[0042] The present invention can coat one layer of heavy metal film 7 on the outer end surface of protrusion 3, as shown in Figure 6, can increase the quality of hard mass center like this, improve the sensitivity of sensor, heavy metal ...
PUM
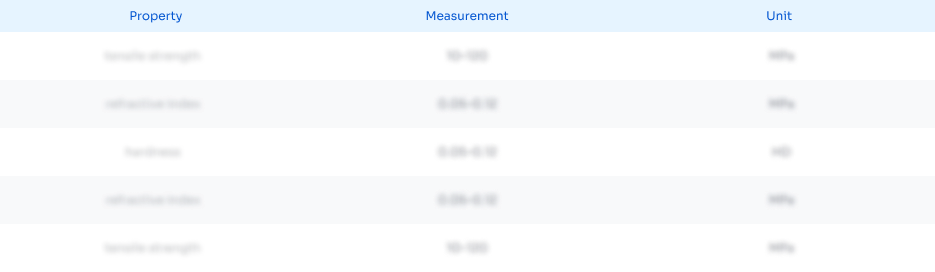
Abstract
Description
Claims
Application Information

- R&D Engineer
- R&D Manager
- IP Professional
- Industry Leading Data Capabilities
- Powerful AI technology
- Patent DNA Extraction
Browse by: Latest US Patents, China's latest patents, Technical Efficacy Thesaurus, Application Domain, Technology Topic, Popular Technical Reports.
© 2024 PatSnap. All rights reserved.Legal|Privacy policy|Modern Slavery Act Transparency Statement|Sitemap|About US| Contact US: help@patsnap.com