High temperature heat integration system for oil-extraction plant and use thereof
A combined system and refinery technology, applied in heat storage heaters, fluid heaters, heat exchanger types, etc., can solve the problems of increasing the fuel consumption of heating furnaces, optimizing matching, and loss of steam, reducing refining costs, The effect of optimizing the heat exchange network and saving medium pressure steam
- Summary
- Abstract
- Description
- Claims
- Application Information
AI Technical Summary
Problems solved by technology
Method used
Image
Examples
Embodiment Construction
[0022] The present invention will be further described below.
[0023]The heat conduction oil at 200-250°C enters the shell side of the fifth heat exchange device 16 newly added in the heat source device 11 through the heat medium pipe, and the heat source that comes out of the bottom outlet of the fractionation tower 6 in the tube side of the fifth heat exchange device 16 The material flow of device 11 is heat exchanged. After the heat exchange, the temperature of the material flow of heat source device 11 is Td=290-260°C. The streams are heat-exchanged, the streams entering the shell side of the first heat exchange equipment 3 are heat-exchanged to Ta=170-230°C, the streams of the heat source device 11 are heat-exchanged to Tb'=280-260°C, and then the streams of the heat source device 11 Then enter the tube side of the second heat exchange equipment 5 and exchange heat with the stream entering the shell side of the second heat exchange equipment 5 until Tc = 270-250 ° C. Aft...
PUM
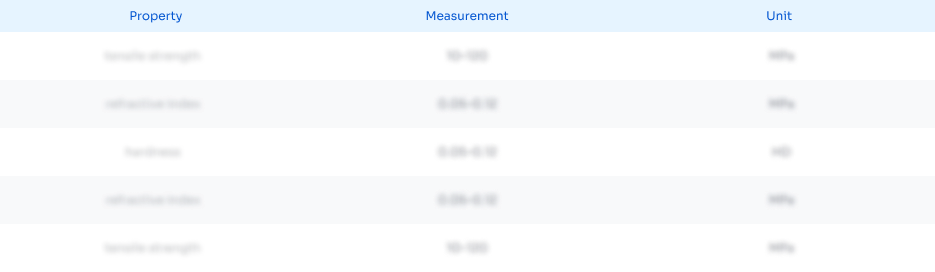
Abstract
Description
Claims
Application Information

- Generate Ideas
- Intellectual Property
- Life Sciences
- Materials
- Tech Scout
- Unparalleled Data Quality
- Higher Quality Content
- 60% Fewer Hallucinations
Browse by: Latest US Patents, China's latest patents, Technical Efficacy Thesaurus, Application Domain, Technology Topic, Popular Technical Reports.
© 2025 PatSnap. All rights reserved.Legal|Privacy policy|Modern Slavery Act Transparency Statement|Sitemap|About US| Contact US: help@patsnap.com