Extractant recovery method and system of technology for preparing adiponitrile trough hydrocyanating allyl acetonitrile
An extraction agent and hydrocyanation technology, applied in organic chemistry, carboxylic acid nitrile purification/separation, etc., to achieve the effect of optimizing heat exchange network, reducing production cost, and realizing effective utilization of energy
- Summary
- Abstract
- Description
- Claims
- Application Information
AI Technical Summary
Problems solved by technology
Method used
Image
Examples
Embodiment 1
[0023] The raffinate A32746kg / h of the adiponitrile extraction process is preheated to 40°C through the third-effect evaporation tower top heat exchanger 8 and enters the first-effect evaporation tower 1. In terms of mass percentage, the raffinate A contains 70% Extractant, 20% catalyst and 10% auxiliary agent. The pressure of the first effect evaporation tower 1 is 200kPaG, and the extraction agent vapor output from the bottom of the first effect evaporation tower 1 enters the second effect evaporation tower 2, the temperature is 130°C, and the pressure is reduced by 70kPa for further decompression evaporation, and then evaporates from the second effect The unevaporated liquid output from the bottom of the tower 2 enters the three-effect evaporation tower 3, the temperature is 115°C, and the pressure is further reduced by 80kPa. Finally, the catalyst and auxiliary agent B are output from the bottom of the three-effect evaporation tower 3, and the extraction agent steam output...
Embodiment 2
[0026] The raffinate A37746kg / h of the adiponitrile extraction process is preheated to 80°C through the third-effect evaporation tower top heat exchanger 8 and enters the first-effect evaporation tower 1. In terms of mass percentage, the raffinate A contains 80% Extractant, 15% catalyst and 5% additives. The pressure of the first-effect evaporation tower 1 is 20kPaG, and the extraction agent vapor output from the bottom of the first-effect evaporation tower 1 enters the second-effect evaporation tower 2, the temperature is 130°C, and the pressure is reduced by 40kPa for further decompression evaporation, and then evaporates from the second effect The unevaporated liquid output from the bottom of the tower 2 enters the three-effect evaporation tower 3, the temperature is 115°C, and the pressure is further reduced by 40kPa. Finally, the catalyst and auxiliary agent B are output from the bottom of the three-effect evaporation tower 3, and the extraction agent steam output from th...
Embodiment 3
[0029] The raffinate A38746kg / h of the adiponitrile extraction process is preheated to 60°C through the top heat exchanger 8 of the third effect evaporation tower and enters the first effect evaporation tower 1. In terms of mass percentage, the raffinate A contains 75% Extractant, 18% catalyst and 7% additives. The pressure of the first-effect evaporation tower 1 is 160kPaG, and the extraction agent vapor output from the bottom of the first-effect evaporation tower 1 enters the second-effect evaporation tower 2, the temperature is 130°C, and the pressure is reduced by 120kPa for further reduced-pressure evaporation, and then evaporated from the second effect The unevaporated liquid output from the bottom of the tower 2 enters the three-effect evaporation tower 3, the temperature is 115°C, and the pressure is further reduced by 40kPa. Finally, the catalyst and auxiliary agent B are output from the bottom of the three-effect evaporation tower 3, and the extraction agent steam ou...
PUM
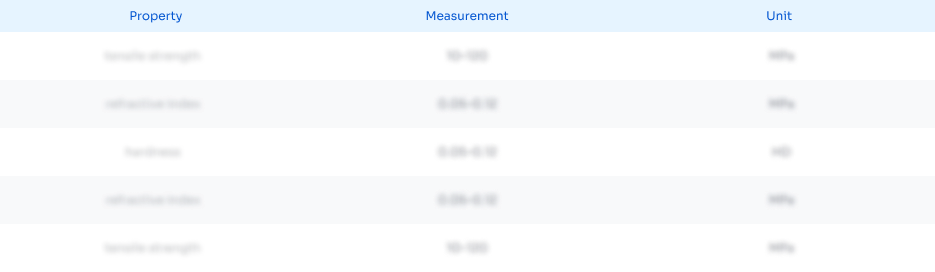
Abstract
Description
Claims
Application Information

- Generate Ideas
- Intellectual Property
- Life Sciences
- Materials
- Tech Scout
- Unparalleled Data Quality
- Higher Quality Content
- 60% Fewer Hallucinations
Browse by: Latest US Patents, China's latest patents, Technical Efficacy Thesaurus, Application Domain, Technology Topic, Popular Technical Reports.
© 2025 PatSnap. All rights reserved.Legal|Privacy policy|Modern Slavery Act Transparency Statement|Sitemap|About US| Contact US: help@patsnap.com