Coal powder pure oxygen blast furnace ironmaking process and equipment thereof
A blast furnace ironmaking and pulverized coal technology, applied in blast furnaces, blast furnace details, blast furnace parts and other directions, can solve problems such as immaturity, and achieve the effects of reducing coal injection costs, good energy-saving effects, and increased production capacity
- Summary
- Abstract
- Description
- Claims
- Application Information
AI Technical Summary
Problems solved by technology
Method used
Image
Examples
Embodiment Construction
[0030] The pulverized coal pure oxygen blast furnace system includes a horizontal hot blast stove 1, an entrained bed gas generator 2, a high-temperature gas composite dust collector 3 and a blast furnace 4 for smelting.
[0031] Entrained bed gas generator 2 is made up of coal injection device and gas generator 28. The coal injection device includes a silo 5 , a first transfer tank 6 , a second transfer tank 7 , an electronic scale 8 , an impeller feeder 9 , and a screw feeder 10 . The upper part of the feed bin 5 is provided with a pulverized coal input port 11, and the lower part of the feed bin 5 is connected with the first transfer tank 6 through a pipeline, and a valve 12 is provided on the pipeline. The first transfer tank 6 is connected to the second transfer tank 7 through pipelines, and a valve 13 is arranged on the connecting pipeline between the first and second transfer tanks. An electronic scale 8 is arranged in the second transfer tank 7 . The lower part of th...
PUM
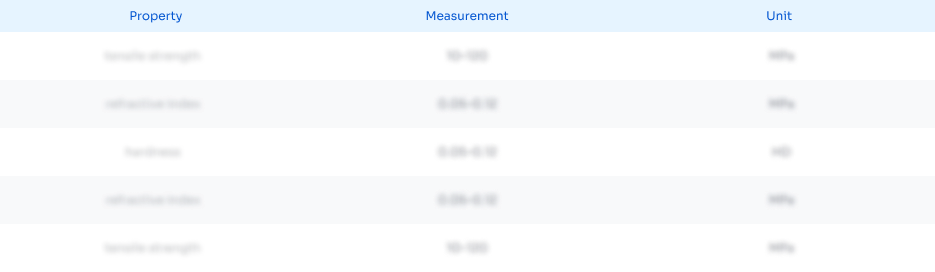
Abstract
Description
Claims
Application Information

- R&D
- Intellectual Property
- Life Sciences
- Materials
- Tech Scout
- Unparalleled Data Quality
- Higher Quality Content
- 60% Fewer Hallucinations
Browse by: Latest US Patents, China's latest patents, Technical Efficacy Thesaurus, Application Domain, Technology Topic, Popular Technical Reports.
© 2025 PatSnap. All rights reserved.Legal|Privacy policy|Modern Slavery Act Transparency Statement|Sitemap|About US| Contact US: help@patsnap.com