Method and system for restoring parent metal properties across welds
A non-destructive, welding material technology used in metal processing, furnaces, heat treatment equipment, etc.
- Summary
- Abstract
- Description
- Claims
- Application Information
AI Technical Summary
Problems solved by technology
Method used
Image
Examples
Embodiment Construction
[0014] An aspect of the present invention, such as but not limiting of the present invention, is to provide a production welding method and related system capable of producing large substantially NDT-indicated castings, such as but not limited to CrMoV castings. The casting may be a sand casting where the manufactured areas have known problems that can be revealed by inspection with non-destructive testing (NDT). These areas that may be indicated by NDT are generally areas less than 1 / 8 inch in size and may include items referred to as incompletes, damages, blemishes, defects, defects, and the like (hereinafter referred to simply as "NDT indications"). These NDT indications are likely due to casting shrinkage during cooling and thermal tearing (cracks) due to the inflexible nature of the core. As recognized, these cores are usually sand with a binder in order to provide shear strength to the core during positioning with a rigid internal framework which provides a structural lo...
PUM
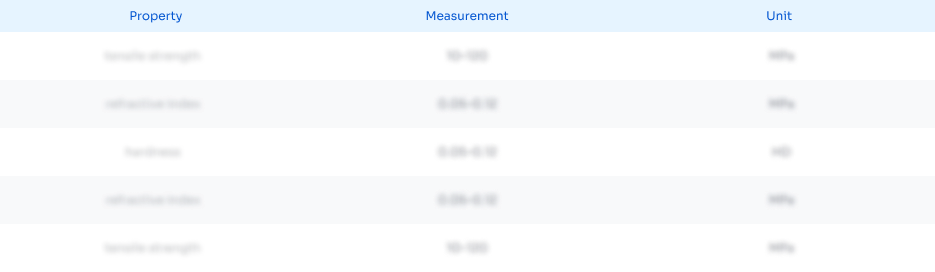
Abstract
Description
Claims
Application Information

- Generate Ideas
- Intellectual Property
- Life Sciences
- Materials
- Tech Scout
- Unparalleled Data Quality
- Higher Quality Content
- 60% Fewer Hallucinations
Browse by: Latest US Patents, China's latest patents, Technical Efficacy Thesaurus, Application Domain, Technology Topic, Popular Technical Reports.
© 2025 PatSnap. All rights reserved.Legal|Privacy policy|Modern Slavery Act Transparency Statement|Sitemap|About US| Contact US: help@patsnap.com