Fuel filter and process for producing a fuel filter
A technology for fuel filters and filter parts, which is applied in chemical instruments and methods, membrane filters, fixed filter element filters, etc., can solve the problems of increased cost, no filtering effect, high cost, etc., and achieves a simple manufacturing solution Effect
- Summary
- Abstract
- Description
- Claims
- Application Information
AI Technical Summary
Problems solved by technology
Method used
Image
Examples
Embodiment Construction
[0028] FIG. 1 shows a sectional illustration of a filter cloth web 1 which is fed as a continuous material from a reel to a not shown injection molding machine. The direction of movement of the filter cloth web is oriented in the plane of the drawing.
[0029] FIG. 2 shows the filter cloth web 1 after leaving the injection molding machine. In an injection molding machine, the two filter elements 2 , 3 are injection-molded onto the filter cloth web 1 adjacent to each other and thus perpendicularly to the direction of movement of the filter cloth web 1 in such a way that the filter cloth 1 substantially covers the filter elements 2 , 3 respective upper surfaces.
[0030] At the same time, the injection-molded pump connection 4 for the subsequent connection to the suction connection of the fuel pump is injected onto the filter element 3 . The region of the two filter elements 2 , 3 lying below the filter cloth web 1 forms the subsequent carrier of the fuel filter 5 .
[0031] ...
PUM
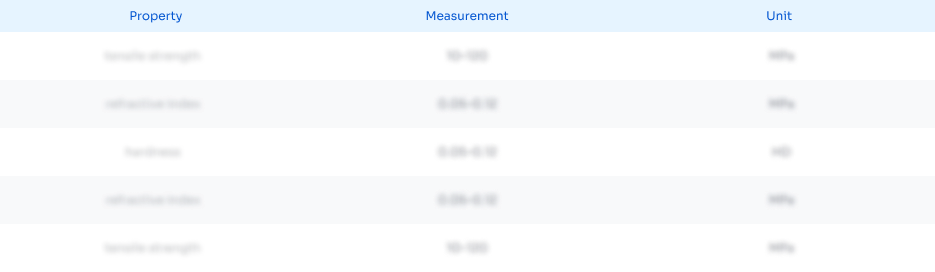
Abstract
Description
Claims
Application Information

- R&D
- Intellectual Property
- Life Sciences
- Materials
- Tech Scout
- Unparalleled Data Quality
- Higher Quality Content
- 60% Fewer Hallucinations
Browse by: Latest US Patents, China's latest patents, Technical Efficacy Thesaurus, Application Domain, Technology Topic, Popular Technical Reports.
© 2025 PatSnap. All rights reserved.Legal|Privacy policy|Modern Slavery Act Transparency Statement|Sitemap|About US| Contact US: help@patsnap.com