Adaptive transmission sensing drive assembly
A drive assembly and self-adaptive technology, applied in engine control, machine/engine, DC motor speed/torque control, etc., can solve problems such as mechanical efficiency loss, stop rotation, lack of road feeling, etc., to improve power performance, Reduced emissions, small size and light weight
- Summary
- Abstract
- Description
- Claims
- Application Information
AI Technical Summary
Problems solved by technology
Method used
Image
Examples
Embodiment Construction
[0032] figure 1It is a schematic structural view of the present invention, as shown in the figure: the power equipment of the present embodiment is a motor, and the direction of rotation of the motor is counterclockwise as viewed from right to left. The motor is arranged outside the box body, the fixed shaft 11 is set inside the box body 23, the part of the right end protruding from the box body 23 is rigidly connected with the motor stator, the left end and the left end cover 12 of the box body 23 are processed into a flat square shaft, and the corresponding left end The cover 12 cooperates with it to form a flat square hole to form a mesh, and is fixed on the box body through the left end cover 12 of the box body. The transmission sleeve 29 is rotatably matched with the fixed shaft 11 through the first radial bearing 38. The left end cover 31 and the right end cover 33 of the motor It is rigidly connected with the motor rotor housing 32 by screws, the right end cover 33 and ...
PUM
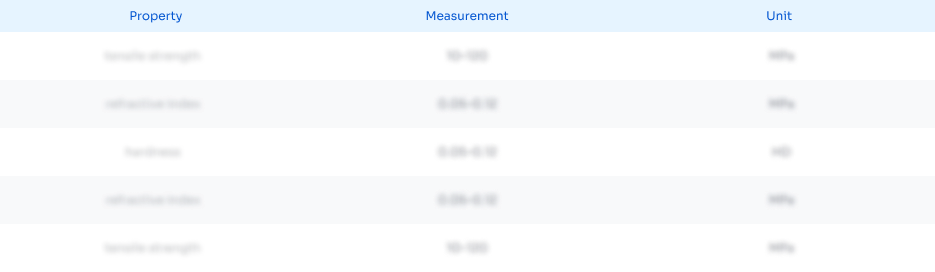
Abstract
Description
Claims
Application Information

- R&D
- Intellectual Property
- Life Sciences
- Materials
- Tech Scout
- Unparalleled Data Quality
- Higher Quality Content
- 60% Fewer Hallucinations
Browse by: Latest US Patents, China's latest patents, Technical Efficacy Thesaurus, Application Domain, Technology Topic, Popular Technical Reports.
© 2025 PatSnap. All rights reserved.Legal|Privacy policy|Modern Slavery Act Transparency Statement|Sitemap|About US| Contact US: help@patsnap.com