Crystallization method of monohydrate glucose
A glucose and crystallization technology, applied in the field of anhydrous glucose production, can solve problems such as difficult control of crystallization temperature, difficulty in separation, waste of glucose monohydrate, etc., reduce the difficulty of purification and impurity removal, improve crystallization effect and quality, save energy and reduce cost-effective effect
- Summary
- Abstract
- Description
- Claims
- Application Information
AI Technical Summary
Problems solved by technology
Method used
Examples
Embodiment 1
[0014] Embodiment 1 Crystallization process when restarting production
[0015] First, in the first crystallization tank, drop into the dry glucose monohydrate that accounts for 2% of the tank volume as a seed crystal, and start feeding. The purity of the feeding sugar solution is 97.5%, the feeding Brix is 72.6, and the feeding temperature is 46 ° C. When After the material is filled with the crystallization tank, stop feeding, start cooling, control the cooling rate of 0.2-0.25°C / hour, uniformly cool down for 18 hours, and the temperature in the tank drops to 41.5°C; then reserve 30% of the volume of the crystallization tank after crystallization. For the seed crystal of the next crystallization, send the remaining material into the second crystallization tank and start to crystallize. The material is cooled at a rate of 0.35-0.5°C / hour for 18 hours. When the temperature of the material drops to 28°C, the cooling is stopped, and the crystallization is completed. Reserve th...
Embodiment 2
[0016] Crystallization process during embodiment 2 continuous production
[0017] In the first and second crystallization tanks, materials accounting for 30% of the tank volume are respectively reserved as seed crystals. Start feeding, the purity of the feeding sugar liquid is 98%, the feeding brix is 72.8, the feeding temperature is 47°C, 10% sodium metabisulfite is added in advance in the sugar liquid, and the SO in the material is recorded. 2 The content is 50ppm. When the material is full of the first crystallization tank, stop feeding and start to cool down. The cooling rate is controlled at 0.3°C / hour, and the temperature is uniformly cooled for 19 hours. The seed crystals of secondary crystallization, and the remaining materials are sent to the second crystallization tank. When the material is full of the second crystallization tank, stop feeding and start to cool down. The material cools down at a rate of 0.3-0.4°C / hour for 16 hours. Stop cooling at ℃, reserve the m...
Embodiment 3
[0018] Crystallization process during embodiment 3 continuous production
[0019] In the first and second crystallization tanks, materials accounting for 36% of the tank volume are respectively reserved as seed crystals. Start feeding, the purity of the feeding sugar liquid is 97%, the feeding hammer is 70.5, and the feeding temperature is 46°C. When the material is full of the first crystallization tank, stop feeding and start cooling, and control the cooling rate at 0.25-0.28°C / Hours, uniform cooling for 18 hours, the temperature drops to 41.0°C, reserve 33% of the volume of the crystallization tank as the seed crystal for the next crystallization, and send the rest of the material into the second crystallization tank, stop when the material is full of the second crystallization tank The feed starts to cool down, and the material cools down at a rate of 0.3-0.35°C / hour for 17 hours. When the temperature of the material drops to 28°C, the cooling is stopped, and the material...
PUM
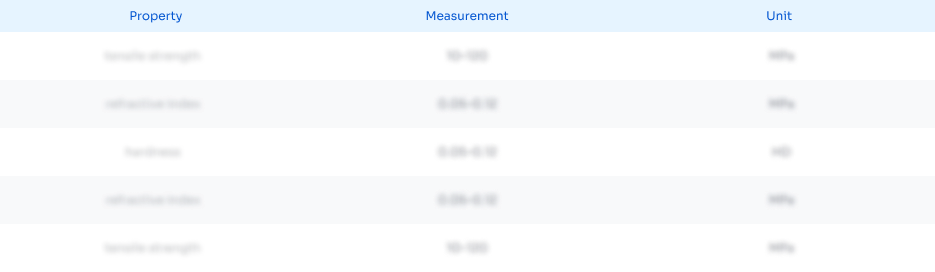
Abstract
Description
Claims
Application Information

- R&D
- Intellectual Property
- Life Sciences
- Materials
- Tech Scout
- Unparalleled Data Quality
- Higher Quality Content
- 60% Fewer Hallucinations
Browse by: Latest US Patents, China's latest patents, Technical Efficacy Thesaurus, Application Domain, Technology Topic, Popular Technical Reports.
© 2025 PatSnap. All rights reserved.Legal|Privacy policy|Modern Slavery Act Transparency Statement|Sitemap|About US| Contact US: help@patsnap.com