Process for the fabrication of a hole
A pulse length, laser technology, applied in the field of hole processing, can solve the problems of small average power of laser pulse, expensive, time-consuming, etc.
- Summary
- Abstract
- Description
- Claims
- Application Information
AI Technical Summary
Problems solved by technology
Method used
Image
Examples
Embodiment Construction
[0025] Description of parts with holes
[0026] figure 1 Part 1 is shown with holes 7 .
[0027] The component 1 is formed from a substrate 4 (for example a casting or a DS or SX component).
[0028] The substrate 4 can be metallic and / or ceramic. Especially in turbine components, such as turbine moving blades 120 or turbine guide vanes 130 ( FIGS. 16 , 17 ), heat shield elements 155 ( Figure 18 ) and other housing components, the substrate 4 is made of a nickel-based, cobalt-based or iron-based superalloy. On turbine blades for aircraft, the substrate 4 is made, for example, of titanium or a titanium-based alloy.
[0029] The substrate 4 has holes 7 which are preferably through-holes. But it can also be a blind hole. The hole 7 comprises a lower region 10 and an upper region 13, the lower region 10 starting from the inner side of the component 1 and preferably symmetrical (such as circular, oval or rectangular) , and the upper region 13 is optionally formed as a dif...
PUM
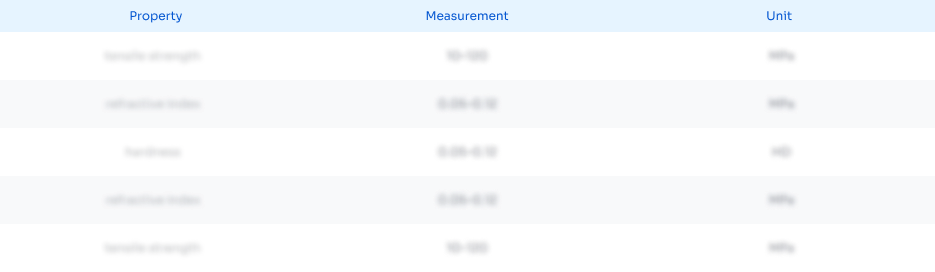
Abstract
Description
Claims
Application Information

- R&D Engineer
- R&D Manager
- IP Professional
- Industry Leading Data Capabilities
- Powerful AI technology
- Patent DNA Extraction
Browse by: Latest US Patents, China's latest patents, Technical Efficacy Thesaurus, Application Domain, Technology Topic, Popular Technical Reports.
© 2024 PatSnap. All rights reserved.Legal|Privacy policy|Modern Slavery Act Transparency Statement|Sitemap|About US| Contact US: help@patsnap.com