Flexible bend pipe core mould
A bending and flexible technology, which is applied in the field of CNC bending molds, can solve the problems that the relative bending radius is not small enough and the structure of the bending mand
- Summary
- Abstract
- Description
- Claims
- Application Information
AI Technical Summary
Problems solved by technology
Method used
Image
Examples
Embodiment 1
[0031] This embodiment is a flexible mandrel for numerical control bending design of a large-diameter thin-walled tube with a diameter of 127mm, a wall thickness of 1.25mm, and a bending radius R of 190.5mm, and its relative bending radius is 1.5D.
[0032] According to the pipe size and bending specifications, it is determined that the outer diameter of the core head body and the core head cover are both 124.02mm, and the number of socket ball joints is 3. This embodiment includes a core head body, a coupling shaft, three socket ball joints, three core head covers and three elastic snap rings.
[0033] The socket and ball joint is an axisymmetric shape. One end of the two socket joints is an inner circular ball socket, and the other end is a sphere. The ball socket is a large semicircle, and its inner diameter is slightly larger than the outer diameter of the ball; on the outer wall of the ball socket mouth, there are positioning steps along the circumference, and there is a...
Embodiment 2
[0046] This embodiment is a flexible mandrel for numerically controlled bending design of a large-diameter thin-walled tube with a diameter of 50mm, a wall thickness of 1mm and a bending radius R of 75mm, and its relative bending radius is 1.5D.
[0047] According to the pipe size and bending specifications, it is determined that the outer diameter of the core head body and the core head cover are both 47.5mm, and the number of socket ball joints is 2. The specific mold design method and assembly method are the same as in Example 1. During the bending process, the flexible core head can be smoothly bent to a bending radius of 1.5 times the pipe diameter, thus ensuring the bending forming with a small bending radius.
[0048] The two socket joints are axisymmetric shapes. One end of one of the socket joints is an inner circular ball socket, and the other end is a sphere. The ball socket is a large semicircle, and its inner diameter is slightly larger than the outer diameter of...
PUM
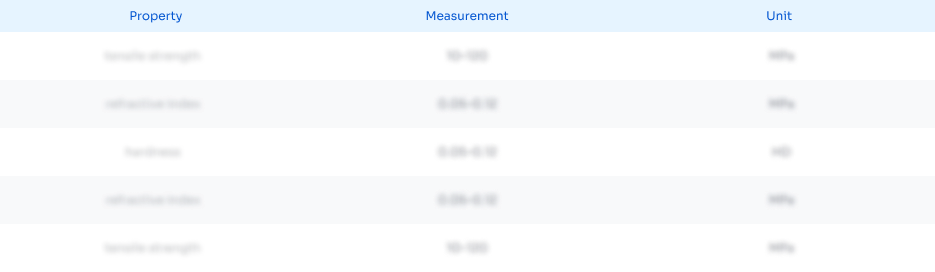
Abstract
Description
Claims
Application Information

- R&D
- Intellectual Property
- Life Sciences
- Materials
- Tech Scout
- Unparalleled Data Quality
- Higher Quality Content
- 60% Fewer Hallucinations
Browse by: Latest US Patents, China's latest patents, Technical Efficacy Thesaurus, Application Domain, Technology Topic, Popular Technical Reports.
© 2025 PatSnap. All rights reserved.Legal|Privacy policy|Modern Slavery Act Transparency Statement|Sitemap|About US| Contact US: help@patsnap.com