Angle-inserting type hot metal pretreatment spray gun
A molten iron pretreatment, oblique insertion technology, applied in the direction of injection devices, liquid injection devices, furnaces, etc., can solve the problems of low service life of the spray gun, poor spray pretreatment effect, etc.
- Summary
- Abstract
- Description
- Claims
- Application Information
AI Technical Summary
Problems solved by technology
Method used
Image
Examples
Embodiment 1
[0017] Such as figure 1 , figure 2 As shown, the present invention comprises a gun core steel pipe 1, a refractory material gun lining 6 and several riveting parts. The angle α is 120 degrees, and the refractory material gun lining 6 is covered on the outer surface of the gun core steel pipe 1, and the outer surface of the gun core steel tube 1 is coated with 98% mechanical lubricating oil and 2% polyester by weight percentage. Burn-out coating 2 composed of propylene powder. The rivet is composed of a V-shaped rivet 3, a double-V butterfly rivet 4 and a ring rivet 5. The height of the V-shaped rivet 3 is 4mm smaller than the thickness of the refractory gun lining 6. The double-V butterfly rivet The height of 4 is 2 / 3 of the thickness of refractory material gun lining 6, the inner diameter of ring rivet 5 is 3.5mm smaller than the thickness of refractory material gun lining 6, V-shaped rivet 3, double V butterfly rivet 4 press the gun core Steel pipes are welded on the out...
Embodiment 2
[0020] The difference between this embodiment and Embodiment 1 is that the angle α between the inclined part of the lower end of the gun core steel pipe 1 and the longitudinal axis of the gun core steel tube 1 is 140 degrees; and 8% polypropylene powder; the height of the V-shaped rivet 3 is 3mm smaller than the thickness of the refractory gun lining 6, the height of the double-V butterfly rivet 4 is 1 / 2 of the thickness of the refractory gun lining 6, and the ring The inner diameter of the rivet 5 is 3mm smaller than the thickness of the refractory gun lining 6, the diameter of the V-shaped rivet 3, the double-V butterfly rivet 4 and the ring rivet 5 are 2.5mm, the V-shaped rivet 3, the double-V butterfly The riveting piece 4 is welded on the outer wall of the gun core steel pipe 1 according to the axial spacing of the gun core steel tube 40mm, 60mm or 80mm.
PUM
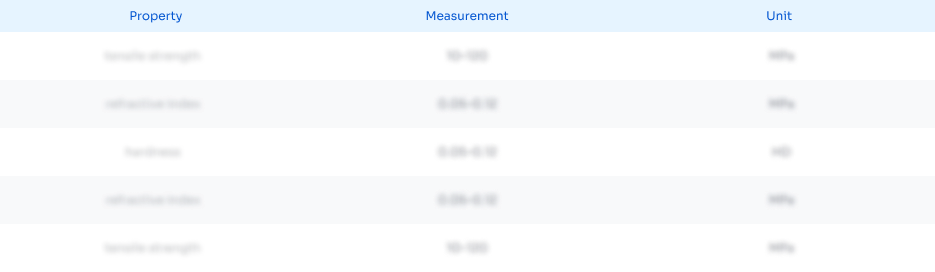
Abstract
Description
Claims
Application Information

- Generate Ideas
- Intellectual Property
- Life Sciences
- Materials
- Tech Scout
- Unparalleled Data Quality
- Higher Quality Content
- 60% Fewer Hallucinations
Browse by: Latest US Patents, China's latest patents, Technical Efficacy Thesaurus, Application Domain, Technology Topic, Popular Technical Reports.
© 2025 PatSnap. All rights reserved.Legal|Privacy policy|Modern Slavery Act Transparency Statement|Sitemap|About US| Contact US: help@patsnap.com