Method for producing ultra-long bamboo wood composite section bar
A technology of composite profiles and manufacturing methods, which is applied in the pretreatment of molding materials, manufacturing tools, wood processing appliances, etc., to achieve the effect of reducing the heterogeneity of all parties
- Summary
- Abstract
- Description
- Claims
- Application Information
AI Technical Summary
Problems solved by technology
Method used
Examples
Embodiment Construction
[0014] The manufacturing process of super-long (the length specification of the profile is 5 meters) bamboo-wood composite profile is as follows:
[0015] Raw material processing: Cut out 5.2-meter-long ultra-long bamboo sections, split them radially into bamboo strips, and remove bamboo green and bamboo bones.
[0016] Degreasing, rolling drying, spraying glue, aging: degreasing (ie heat treatment) is soaking chemical raw materials in high temperature water, softening and degreasing treatment, in order to achieve the purpose of softening, anti-corrosion, and mildew prevention; rolling is to press the raw materials into unequal cracks The green sheet has a thickness of 0.3-0.4cm and a width of 1.7-2.0cm, and is dried so that the moisture content of the bamboo strips is controlled at 8-12%; 30-32%, the amount of dipping is 20-22%, and the surface of the slab is impregnated with preservatives; aging refers to placing the raw materials after gluing for a period of time to make th...
PUM
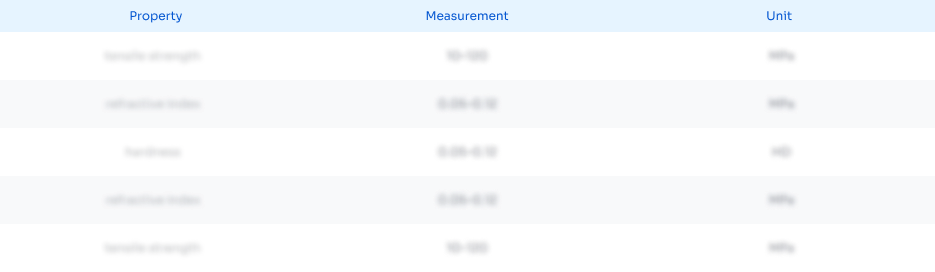
Abstract
Description
Claims
Application Information

- R&D
- Intellectual Property
- Life Sciences
- Materials
- Tech Scout
- Unparalleled Data Quality
- Higher Quality Content
- 60% Fewer Hallucinations
Browse by: Latest US Patents, China's latest patents, Technical Efficacy Thesaurus, Application Domain, Technology Topic, Popular Technical Reports.
© 2025 PatSnap. All rights reserved.Legal|Privacy policy|Modern Slavery Act Transparency Statement|Sitemap|About US| Contact US: help@patsnap.com