Method for producing G group plate mode steel plate by the combination of digital control torch cutter and shears
A shearing machine, fire cutting machine technology, applied in shearing device, shearing machine equipment, gas flame welding equipment and other directions, can solve the problems of high production efficiency and low cutting efficiency, and achieve flexible and sufficient arrangement, which is beneficial to thick plates. The effect of yield and contract fulfillment capacity
- Summary
- Abstract
- Description
- Claims
- Application Information
AI Technical Summary
Problems solved by technology
Method used
Image
Examples
Embodiment 1
[0029] Take the shearing line of Baosteel Heavy Plate Plant as an example:
[0030] The production process and time-consuming situation of the original G group plate mode steel plate is: G group plate rolled large plate 6 is hoisted into the surface of the CNC cutting machine by a crane, it takes 5 minutes; the CNC cutting machine scans the steel plate and automatically sets the material to determine the cutting path , it takes 10 minutes; the CNC cutting machine cuts according to the set cutting path, and it takes 2 hours; the finished steel plate is hoisted from the surface of the CNC cutting machine by a crane, and it takes 15 minutes. It usually takes 15 minutes to cut a G group plate mode steel plate. More than 2.5 hours.
[0031] see figure 1 It is a necessary condition for the realization of this technology that the thick plate shearing line and the CNC flame cutting machine are arranged within the same workshop span. Such equipment arrangement provides the possibility...
Embodiment 2
[0047] Except in this embodiment, the value of the splitting slit width is as follows:
[0048] Steel plate thickness (mm)
Slit width(mm)
0~10
1.00-1.10
10~20
1.50-1.60
20~40
2.60-2.70
40~50
3.50-3.60
[0049] Except that the shear margin is set at 8-10 mm, the others are the same as in Embodiment 1, and the method of combining the numerical control fire cutting machine and the shearing machine of the present invention to produce the G group plate model steel plate is carried out.
[0050] As mentioned above, according to the method of combining the numerical control fire cutting machine and the shearing machine in the above two embodiments to produce the G-group pattern steel plate, according to the original G-group pattern steel plate production process, it usually takes 2.5 hours to cut a G-group pattern steel plate in total. Above, and in the above-mentioned embodiment, the cutting process of t...
PUM
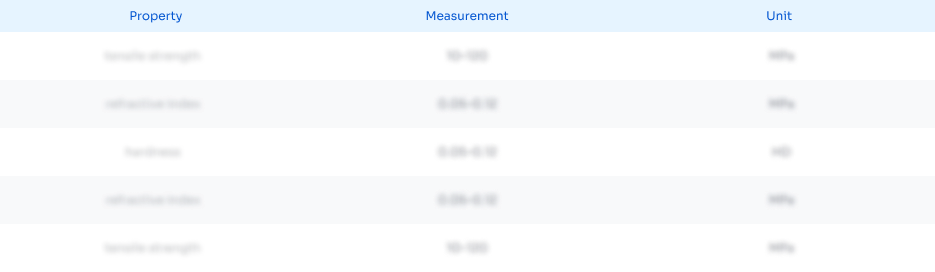
Abstract
Description
Claims
Application Information

- R&D Engineer
- R&D Manager
- IP Professional
- Industry Leading Data Capabilities
- Powerful AI technology
- Patent DNA Extraction
Browse by: Latest US Patents, China's latest patents, Technical Efficacy Thesaurus, Application Domain, Technology Topic, Popular Technical Reports.
© 2024 PatSnap. All rights reserved.Legal|Privacy policy|Modern Slavery Act Transparency Statement|Sitemap|About US| Contact US: help@patsnap.com