Non-linear temperature compensation method for digital sound wave variable density sonic system
A technology of temperature compensation and variable density, which is applied in the direction of earthwork drilling, measurement, borehole/well components, etc., and can solve the problem that it is difficult to obtain satisfactory and qualified transducers
- Summary
- Abstract
- Description
- Claims
- Application Information
AI Technical Summary
Problems solved by technology
Method used
Image
Examples
Embodiment
[0016] Such as figure 1 , 2 As shown, a digital acoustic variable density non-linear temperature compensation logging tool, the temperature sensor 3 is installed in the acoustic system 2, and its calibration and logging process are controlled by the single-chip microcomputer in the variable density electronic circuit 1. Put a newly installed acoustic wave variable density logging tool in the high-temperature and high-pressure simulation well 4. First, the temperature of the simulation well is raised from normal temperature to 160°C repeatedly to test the piezoelectric crystal transducer used in the acoustic system several times. Temperature aging test. After the piezoelectric crystal transducer is subjected to the temperature aging test, the instrument issues a calibration command to calibrate the digital sound wave variable density, and the whole process is automatically recorded by the single-chip microcomputer. The specific process is as follows:
[0017] 1. The single-c...
PUM
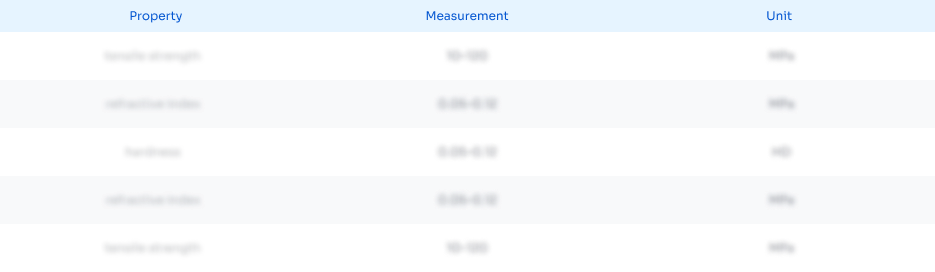
Abstract
Description
Claims
Application Information

- R&D
- Intellectual Property
- Life Sciences
- Materials
- Tech Scout
- Unparalleled Data Quality
- Higher Quality Content
- 60% Fewer Hallucinations
Browse by: Latest US Patents, China's latest patents, Technical Efficacy Thesaurus, Application Domain, Technology Topic, Popular Technical Reports.
© 2025 PatSnap. All rights reserved.Legal|Privacy policy|Modern Slavery Act Transparency Statement|Sitemap|About US| Contact US: help@patsnap.com