Rolling method of large size round steel
A technology for large-sized, round steel, applied in the field of rolling of large-sized round steel, can solve the problems of poor forging surface quality and precision, restricting continuous production, affecting the quality of finished steel, etc. Crack defect, low rolling cost effect
- Summary
- Abstract
- Description
- Claims
- Application Information
AI Technical Summary
Problems solved by technology
Method used
Image
Examples
Embodiment Construction
[0027] Below in conjunction with accompanying drawing, the present invention is described in detail with rolling Φ 250mm round steel.
[0028] Roll the Φ250mm round steel with a Φ500mm round billet, send the round billet into the furnace and heat it to about 1200 degrees according to the conventional method. Shape casting billet, sent to the two-roller reversible blanking machine to open the billet (such as figure 1 , figure 2 As shown, the guide plate has been extended to the vicinity of the pass of the roll), the steel is turned after one pass, and then the steel is turned once every three passes, and the steel is turned once every two passes, a total of 10 passes are rolled, and the rolling is completed. The finished steel billet is 255mm in height and 273mm in width; then, the billet is sent to the continuous rolling mill for rolling. 1.3, that is to get Φ250mm finished round steel.
[0029] The pass system of the blanking machine is a box-box pass, the pass side wall ...
PUM
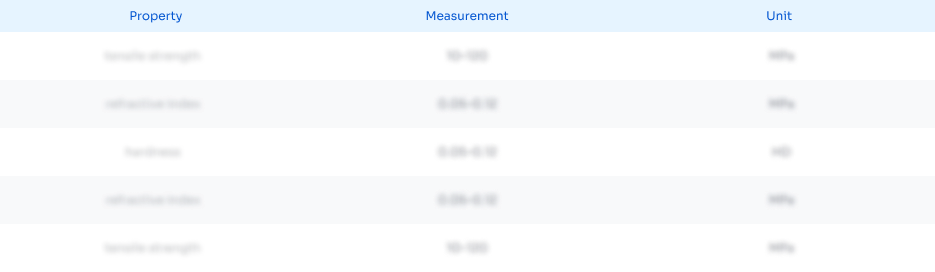
Abstract
Description
Claims
Application Information

- R&D
- Intellectual Property
- Life Sciences
- Materials
- Tech Scout
- Unparalleled Data Quality
- Higher Quality Content
- 60% Fewer Hallucinations
Browse by: Latest US Patents, China's latest patents, Technical Efficacy Thesaurus, Application Domain, Technology Topic, Popular Technical Reports.
© 2025 PatSnap. All rights reserved.Legal|Privacy policy|Modern Slavery Act Transparency Statement|Sitemap|About US| Contact US: help@patsnap.com