Leaf spring consisting of a fibre-composite material
A fiber composite material, leaf spring technology, used in vehicle springs, springs/shock absorbers, leaf springs, etc., can solve problems such as insufficient outflow, insufficient longitudinal extension and orientation of fibers, and reduced load characteristics of leaf springs, to avoid blocking effect
- Summary
- Abstract
- Description
- Claims
- Application Information
AI Technical Summary
Problems solved by technology
Method used
Image
Examples
Embodiment Construction
[0032] The leaf spring 1 shown in the schematic plan view according to FIGS. 4 and 5 is provided for a likewise not shown wheel suspension of a motor vehicle not shown. The leaf spring is made from a large number of unidirectional fiber layers impregnated with resin and placed on top of each other, or from prefabricated prepregs, which are pressed during the manufacturing process. The molds are interconnected in a known manner. The two leaf springs 1 have unidirectional first fibers 6 which extend from the axial end 5 without being severed as far as the opposite axial end 5 . Furthermore, the leaf spring 1 is provided with unidirectional second fibers 7 which extend only over a part of the length of the leaf spring, preferably over the fastening area, and which extend to the axial end 5 with different spacing.
[0033] The first fibers 6 and the second fibers 7 or the prepregs containing the first fibers 6 or the second fibers 7 are preferably cut from the same continuously ...
PUM
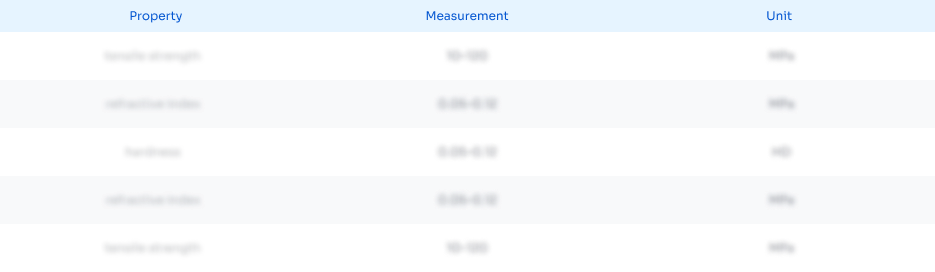
Abstract
Description
Claims
Application Information

- R&D Engineer
- R&D Manager
- IP Professional
- Industry Leading Data Capabilities
- Powerful AI technology
- Patent DNA Extraction
Browse by: Latest US Patents, China's latest patents, Technical Efficacy Thesaurus, Application Domain, Technology Topic, Popular Technical Reports.
© 2024 PatSnap. All rights reserved.Legal|Privacy policy|Modern Slavery Act Transparency Statement|Sitemap|About US| Contact US: help@patsnap.com