Method for preparing lithium carbonate by extracting lithium from lepidolite
A lepidolite and lithium carbonate technology, applied in the direction of lithium carbonate;/acid carbonate, etc., can solve the problems of large material flow, low recovery rate, high limestone ratio, etc. Reduction, the effect of high lithium concentration
Active Publication Date: 2008-11-12
GANFENG LITHIUM CO LTD
View PDF0 Cites 51 Cited by
- Summary
- Abstract
- Description
- Claims
- Application Information
AI Technical Summary
Problems solved by technology
Although this method is better than the lime roasting method, there are still the following problems: (1) potassium sulfate consumption is large, resulting in higher production costs
However, there is a high proportion of limestone, which requires a large amount of limestone to be decomposed in the rotary kiln (about 40 tons of
Method used
the structure of the environmentally friendly knitted fabric provided by the present invention; figure 2 Flow chart of the yarn wrapping machine for environmentally friendly knitted fabrics and storage devices; image 3 Is the parameter map of the yarn covering machine
View moreImage
Smart Image Click on the blue labels to locate them in the text.
Smart ImageViewing Examples
Examples
Experimental program
Comparison scheme
Effect test
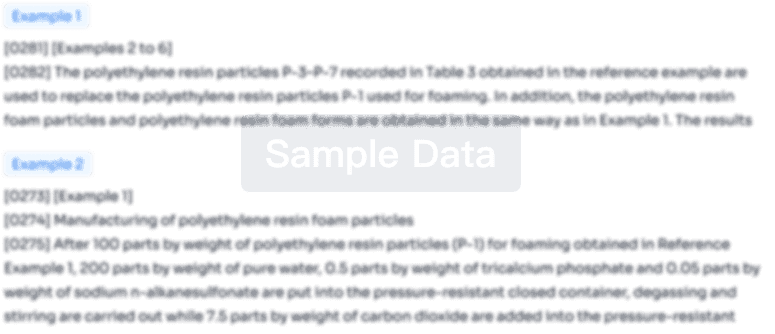
PUM
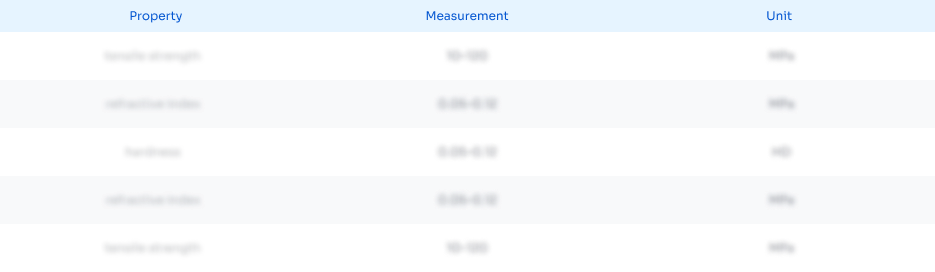
Abstract
The invention relates to a method for preparing lithium carbonate by extracting lithium from lepidolite. The method comprises the following steps of: a. calcination and defluorination at a high temperature; b. grinding; c. autoclaving; d. impurity removal; e. condensation; f. sodium separation by freezing; g. ithium precipitation by carbonization, wherein, in the step c, the grinded lepidolite, calcium oxide and sodium salt are thrown into a high-pressure kettle for autoclaving; the lepidolite is decomposed in the continuous stirring state; and alkali metal in the lepidolite is subject to ion exchange, turned into salt and dissolved out. In the step d, an autoclaving mother solution and autoclaving residues are obtained after separation and autoclaving; sodium hudroxide with slightly excess amount according to the Lithia content in the autoclaving mother solution is added and evenly stirred, then activated carbon is added for filtering and impurity removal. In the step g, CO2 is led to a sodium separation mother solution till the PH value of the solution is equal to between 9 and 10; the mother solution is heated, stirred, carbonized and subject to centrifugal water spinning and separation to obtain coarse lithium carbonate; backwashing and drying are carried out to the coarse lithium carbonate, thereby obtaining a product of lithium carbonate. The method has the advantages that: the method has high lithium yield rate; residues can be utilized; and sodium salt can be recycled, etc.
Description
Technical field [0001] The invention relates to the field of chemical industry, and in particular to a method for extracting lithium from lepidolite to prepare lithium carbonate. Background technique [0002] Lepidolite in Yichun, Jiangxi Province is the largest lithium resource that has been proven and developed so far in my country. Its reserves account for 10.14% of the country's resource reserves and 84.9% of the country's mined lithium ore reserves. Li in Yichun Lepidolite Concentrate 2 The O content is generally around 4.5%, and it also contains Rb 2 O.Cs 2 O.K. 2 O and other useful minerals, how to develop this resource is of great significance to my country's lithium industry. [0003] Currently, the main research methods for extracting lithium from lepidolite include lime milk pressure cooking method, sulfate method and limestone roasting method. The lime milk pressure cooking method is to grind lepidolite to 200 mesh, directly add water and calcium hydroxide, ...
Claims
the structure of the environmentally friendly knitted fabric provided by the present invention; figure 2 Flow chart of the yarn wrapping machine for environmentally friendly knitted fabrics and storage devices; image 3 Is the parameter map of the yarn covering machine
Login to View More Application Information
Patent Timeline

IPC IPC(8): C01D15/08
Inventor 李良彬胡耐根黄学武彭爱平朱时贵葛钰玮邹海平
Owner GANFENG LITHIUM CO LTD
Features
- R&D
- Intellectual Property
- Life Sciences
- Materials
- Tech Scout
Why Patsnap Eureka
- Unparalleled Data Quality
- Higher Quality Content
- 60% Fewer Hallucinations
Social media
Patsnap Eureka Blog
Learn More Browse by: Latest US Patents, China's latest patents, Technical Efficacy Thesaurus, Application Domain, Technology Topic, Popular Technical Reports.
© 2025 PatSnap. All rights reserved.Legal|Privacy policy|Modern Slavery Act Transparency Statement|Sitemap|About US| Contact US: help@patsnap.com