Boiler flue gas recycling method
A boiler flue gas and flue gas technology, applied in the direction of combustion methods, furnaces, furnace types, etc., can solve problems such as difficulty in meeting the national flue gas emission standards, energy waste, pollution, etc., and achieve improved atmospheric environment quality, reduced smoke and dust content, The effect of energy consumption reduction
- Summary
- Abstract
- Description
- Claims
- Application Information
AI Technical Summary
Problems solved by technology
Method used
Image
Examples
Embodiment 1
[0011] 35t / d steam ton combustion boiler, after the flue gas passes through the electrostatic precipitator, the air volume is 10×10 5 Meter 3 / hour, the temperature of the flue gas is 150°C, and it is mixed with the hot air generated by the combustion of the gas generator burner, so that the mixed hot air and the modified lignin are in contact with two Φ8012 mm high-speed centrifugal spray drying towers, and the temperature of the mixed hot air is 250°C. The modified lignin products are produced, and the operating conditions are stable. The indicators of the tested flue gas are as follows:
[0012]
[0013] Nitrogen oxides were not detected, and the modified lignin product was tested to meet the quality requirements of the national standard GB8076-1997 ordinary water reducer first-grade product.
Embodiment 2
[0015] 20t / d steam ton heating boiler, the air volume after electrostatic dust removal is 5×10 4 Meter 3 / hour, the temperature of the flue gas after electrostatic dust removal is 160 °C, and it is mixed with the hot air generated by the combustion of the gas generator burner, so that the mixed hot air and the modified lignin are in contact with a Φ8012 mm high-speed centrifugal spray drying tower, and the temperature of the mixed hot air The temperature is 350°C, and the modified lignin product is produced. The indicators of the tested flue gas are as follows:
[0016]
[0017] Nitrogen oxides were not detected, and the modified lignin product was tested to meet the quality requirements of the national standard GB8076-1997 ordinary water reducer first-grade product.
PUM
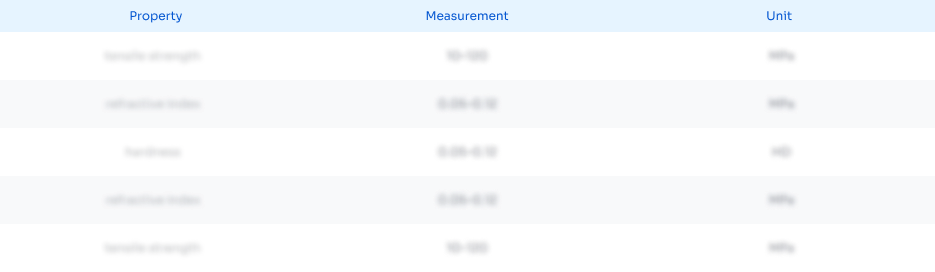
Abstract
Description
Claims
Application Information

- Generate Ideas
- Intellectual Property
- Life Sciences
- Materials
- Tech Scout
- Unparalleled Data Quality
- Higher Quality Content
- 60% Fewer Hallucinations
Browse by: Latest US Patents, China's latest patents, Technical Efficacy Thesaurus, Application Domain, Technology Topic, Popular Technical Reports.
© 2025 PatSnap. All rights reserved.Legal|Privacy policy|Modern Slavery Act Transparency Statement|Sitemap|About US| Contact US: help@patsnap.com