Process for making bricks by waste residue of smelting chromium irons
A ferrochromium alloy and waste slag technology is applied in the technological field of smelting ferrochromium alloy waste slag to make bricks, which can solve the problems of unattended solid waste, pollute the ecological environment, and limited compressive strength, and save cement consumption, natural resources, and price. low cost effect
Inactive Publication Date: 2008-10-22
钱海华
View PDF0 Cites 11 Cited by
- Summary
- Abstract
- Description
- Claims
- Application Information
AI Technical Summary
Problems solved by technology
Due to its long solidification time and limited bearing strength, it is no longer suitable for the current construction market demand, so it becomes solid waste and no one cares about it, seriously polluting the ecological environment
Method used
the structure of the environmentally friendly knitted fabric provided by the present invention; figure 2 Flow chart of the yarn wrapping machine for environmentally friendly knitted fabrics and storage devices; image 3 Is the parameter map of the yarn covering machine
View moreImage
Smart Image Click on the blue labels to locate them in the text.
Smart ImageViewing Examples
Examples
Experimental program
Comparison scheme
Effect test
Embodiment Construction
the structure of the environmentally friendly knitted fabric provided by the present invention; figure 2 Flow chart of the yarn wrapping machine for environmentally friendly knitted fabrics and storage devices; image 3 Is the parameter map of the yarn covering machine
Login to View More PUM
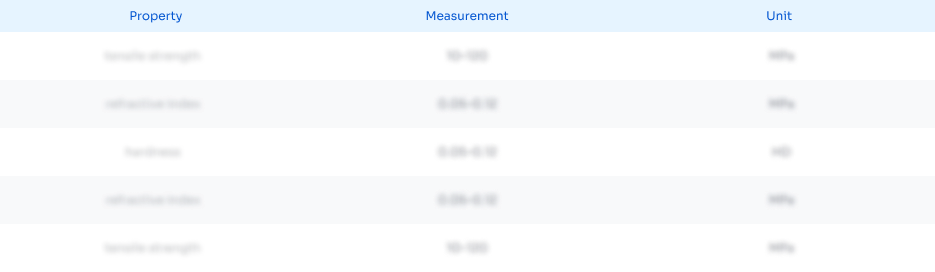
Abstract
The invention relates to a technique using the waste residue of smelted chromium-iron alloy for brick making, the steps thereof are as follows: the mass mixture ratio of various raw materials is: 3.5 to 3 portions of cement, 17 to 24 portions of slag, 65 to 70 portions of fillers, 0.05 to 0.1 portion of an activator and the ratio of water to water / powder is equal to 0.3, wherein, the powder quantity is gauged by the mixing quantity of the cement and the powder residue; the slag and the filler are firstly added into a stirrer to be stirred for 60 seconds and 1 / 2 of the water amount is added and stirred for 60 seconds, and then the cement and the activator are added to be stirred for 3 minutes. In the stirring process, water is added and water usage is well controlled to form the shape of slime. The mixture taking the shape of slime is fed into the charging hopper of a vibrating brick making machine and the feeding vibration is carried out for 8S to 10S and the compression vibration is carried out for 10S to 12S, and then the mixture is molded and taken out to be piled up; after 24 hours, the mixture is maintained by watering. The invention has the advantages that: 1. precious territorial resources can be saved; 2. the usage of the cement can be saved so as to have the advantage in the building materials market with low cost; 3. the slag is comprehensively utilized, thereby changing waste into valuable and also having good environmental benefits.
Description
A technology for making bricks with waste slag from smelting ferrochrome alloy technical field The invention relates to the field of brick making, and mainly relates to a technology for making bricks by using waste slag from smelting ferrochrome alloy. Background technique At present, most of the bricks used in construction are fired bricks (red bricks) and unfired bricks. to make. Unburned bricks are mixed with cement, sand, stone (aggregate) and water to form a slurry, which is vibrated by a vibrating brick making machine into solid bricks and hollow bricks. Both types of bricks consume a lot of natural resources. In ferroalloy smelting enterprises, wastes discharged during the process of smelting medium, low and micro-carbon ferrochromium ferrochrome alloys with refining furnaces are commonly known as chromium slag. From the analysis of chemical composition, the main components of chromium ore smelting slag are (mass percentage): SiO2: 34, Mgo: 16, CaO: 32, k2O: 6Na...
Claims
the structure of the environmentally friendly knitted fabric provided by the present invention; figure 2 Flow chart of the yarn wrapping machine for environmentally friendly knitted fabrics and storage devices; image 3 Is the parameter map of the yarn covering machine
Login to View More Application Information
Patent Timeline

IPC IPC(8): C04B28/00C04B18/14
CPCC04B28/02C04B2111/00017Y02W30/91C04B14/00C04B18/144C04B40/0067
Inventor 钱海华
Owner 钱海华
Features
- R&D
- Intellectual Property
- Life Sciences
- Materials
- Tech Scout
Why Patsnap Eureka
- Unparalleled Data Quality
- Higher Quality Content
- 60% Fewer Hallucinations
Social media
Patsnap Eureka Blog
Learn More Browse by: Latest US Patents, China's latest patents, Technical Efficacy Thesaurus, Application Domain, Technology Topic, Popular Technical Reports.
© 2025 PatSnap. All rights reserved.Legal|Privacy policy|Modern Slavery Act Transparency Statement|Sitemap|About US| Contact US: help@patsnap.com