Outer rotor type permanent magnetism synchronization gear wheel free traction machine
A technology of gear traction machine and permanent magnet synchronization, which is applied in the field of traction machine, can solve the problems of out-of-tolerance runout of the groove surface of the traction wheel, non-concentricity of the rotor and the shaft, and runout of the outer surface of the rotor, so as to achieve small surface runout, The effect of low machine height and high rotor concentricity
- Summary
- Abstract
- Description
- Claims
- Application Information
AI Technical Summary
Problems solved by technology
Method used
Image
Examples
Embodiment Construction
[0012] The present invention will be further described below in conjunction with accompanying drawing and embodiment:
[0013] The structure of an outer rotor type permanent magnet synchronous gearless traction machine of the present invention is as follows: figure 2 As shown, its structure is mainly composed of shaft 1, front bearing 2, spoke 5, traction wheel 7, outer rotor 9, inner stator 10, frame 11, rear bearing 12, and brake 13. The inner stator 10 is fastened and installed on the machine. The outer rotor 9 is located outside the stator 10 and fixed on the right end of the spoke 5 by the rotor screw 8 on the support sleeve protruding from the inside of the seat 11, and the traction wheel 7 is fixed on the left end of the spoke 5, and the shaft 1 and the spoke 5 are integrally cast The structure is supported by the front bearing 2 and the rear bearing 12 installed in the frame. Since the shaft 1 and the spoke 5 are integrally structured, they are processed together dur...
PUM
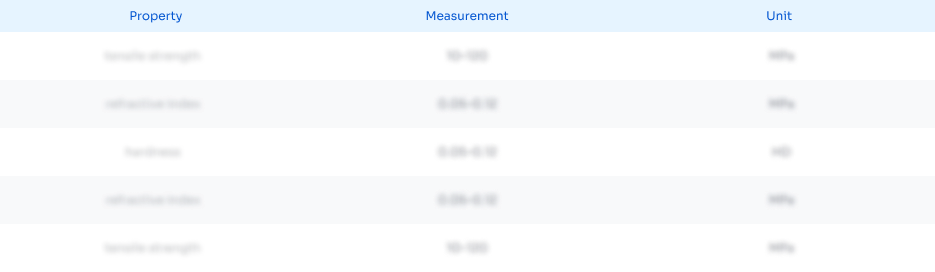
Abstract
Description
Claims
Application Information

- R&D Engineer
- R&D Manager
- IP Professional
- Industry Leading Data Capabilities
- Powerful AI technology
- Patent DNA Extraction
Browse by: Latest US Patents, China's latest patents, Technical Efficacy Thesaurus, Application Domain, Technology Topic, Popular Technical Reports.
© 2024 PatSnap. All rights reserved.Legal|Privacy policy|Modern Slavery Act Transparency Statement|Sitemap|About US| Contact US: help@patsnap.com