Energy-saving vibration-reduction type flux amplification valve
A flow amplification and throttling groove technology, which is applied in fluid pressure actuators, servo motor components, mechanical equipment, etc., can solve the problems of ineffective unloading of steering hydraulic pumps, poor operating comfort of construction machinery, and poor performance of flow amplification valves, etc. problems, to achieve excellent vibration damping effect, strong resistance to oil pollution, and prolong service life
- Summary
- Abstract
- Description
- Claims
- Application Information
AI Technical Summary
Problems solved by technology
Method used
Image
Examples
Embodiment Construction
[0008] Such as Figure 1 ~ Figure 4 As shown, the energy-saving and vibration-reducing flow amplifying valve 1 includes a hydraulic proportional directional valve 2, a safety valve 3, and a differential overflow valve 4, and the hydraulic proportional directional valve 2 includes a main valve core 5, a small valve core 13, a spring 7, small valve spring 16, valve body 12, right valve cover 10, left valve cover 11. The main valve core 5 is kept in the middle position of the valve body 12 by the retaining ring 6, the spring 7, the spring seat 8, the hollow screw 9, and the right valve cover 10. The small valve core 13 in the main valve core 5 is formed by the small valve retaining ring 15, Small valve spring 16, screw 17, small valve spring seat 18, screw plug 19 are kept in the middle position in the main valve core 5, and there are four throttling groove groups in the middle of the main valve core 5, and the four throttle groove groups are about the main valve core 5. The SS ...
PUM
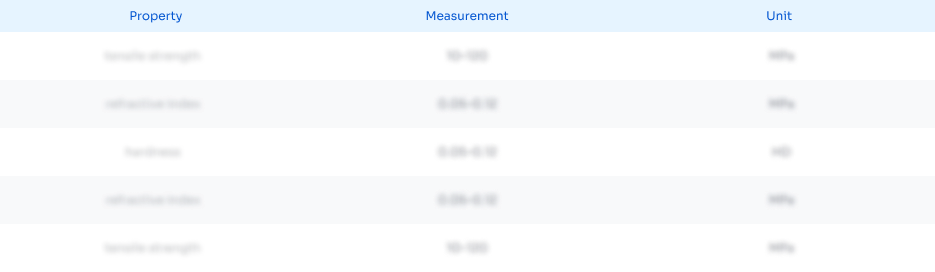
Abstract
Description
Claims
Application Information

- R&D
- Intellectual Property
- Life Sciences
- Materials
- Tech Scout
- Unparalleled Data Quality
- Higher Quality Content
- 60% Fewer Hallucinations
Browse by: Latest US Patents, China's latest patents, Technical Efficacy Thesaurus, Application Domain, Technology Topic, Popular Technical Reports.
© 2025 PatSnap. All rights reserved.Legal|Privacy policy|Modern Slavery Act Transparency Statement|Sitemap|About US| Contact US: help@patsnap.com