Control system for seabed processing system
A control system and processing unit technology, applied in wellbore/well components, construction, production fluids, etc., can solve the problems of expensive, unmeasured hydrocarbon product composition analysis, etc.
- Summary
- Abstract
- Description
- Claims
- Application Information
AI Technical Summary
Problems solved by technology
Method used
Image
Examples
Embodiment Construction
[0020] Referring to Figures 1 and 2 of the accompanying drawings, the drawings show the installation of the subsea processing system (100). The subsea processing system (100) generally has a main platform (140), which may be, for example, on land or on a fixed or floating drilling platform. The master platform (140) has a master control station (150) connected to the first system-module (110) through a communication line (141). The first system-module (110) comprises a control unit (60) connected to an actuating device (121) via a control line (122). The first system-module (110) is lowered to the docking-manifold (130) by means of installation tools such as Remotely Operated Vehicles (ROVs) or by ship or directly from the main platform (140). The first system-module (110) is then connected to the docking-manifold (130) through a multi-bore fluid connector. The actuator (121) on the system-module (110) aligns and engages in place with the diverter valve (131) on the dock-man...
PUM
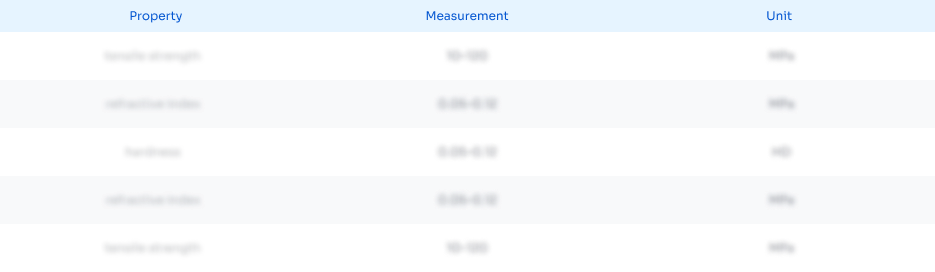
Abstract
Description
Claims
Application Information

- R&D Engineer
- R&D Manager
- IP Professional
- Industry Leading Data Capabilities
- Powerful AI technology
- Patent DNA Extraction
Browse by: Latest US Patents, China's latest patents, Technical Efficacy Thesaurus, Application Domain, Technology Topic, Popular Technical Reports.
© 2024 PatSnap. All rights reserved.Legal|Privacy policy|Modern Slavery Act Transparency Statement|Sitemap|About US| Contact US: help@patsnap.com