Driving apparatus
A technology of driving device and driven body, applied in the direction of installation, generator/motor, piezoelectric effect/electrostrictive or magnetostrictive motor, etc., can solve the problem of inability to ensure impact resistance, displacement suppression unit collision, Problems such as destroying piezoelectric elements
- Summary
- Abstract
- Description
- Claims
- Application Information
AI Technical Summary
Problems solved by technology
Method used
Image
Examples
Embodiment Construction
[0027] The driving device of the present invention includes: a bending displacement member; and a control unit for electrically controlling the bending displacement of the bending displacement member. That is, in the drive device, the bending displacement of the bending displacement member can be excited by electrical control by the control unit. First, a bending displacement member that excites bending displacement by electrical control will be described. As an example of the bending displacement member, a piezoelectric element having a bimorph structure as shown in FIGS. 5( a ) and 5 ( b ) is mentioned.
[0028] FIG. 5( a ) is a side view showing the structure of a piezoelectric element having a bimorph structure, and FIG. 5( b ) is a diagram showing a state of bending displacement of the piezoelectric element.
[0029] The piezoelectric element shown in FIG. 5(a) and FIG. 5(b) has: two piezoelectric material layers 22X·22Y, and a spacer (vibration plate) 21 made of metal, ...
PUM
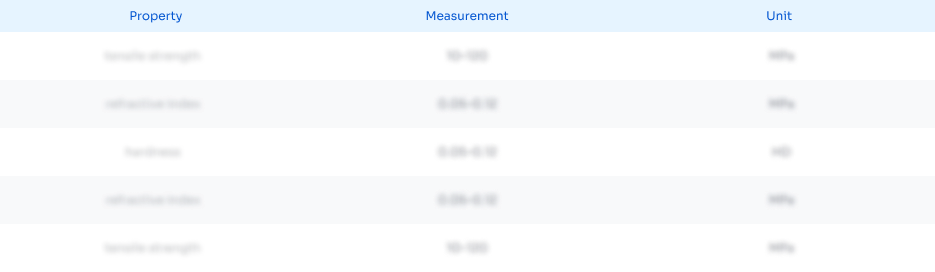
Abstract
Description
Claims
Application Information

- R&D
- Intellectual Property
- Life Sciences
- Materials
- Tech Scout
- Unparalleled Data Quality
- Higher Quality Content
- 60% Fewer Hallucinations
Browse by: Latest US Patents, China's latest patents, Technical Efficacy Thesaurus, Application Domain, Technology Topic, Popular Technical Reports.
© 2025 PatSnap. All rights reserved.Legal|Privacy policy|Modern Slavery Act Transparency Statement|Sitemap|About US| Contact US: help@patsnap.com