Control method and device for actively changing stiffness by inhaul cable vibration
A technology of stiffness control and active control, applied in electric controllers, building components, shockproof, etc., can solve problems such as unsatisfactory control effects, achieve significant comprehensive benefits and improve safety guarantees
- Summary
- Abstract
- Description
- Claims
- Application Information
AI Technical Summary
Problems solved by technology
Method used
Image
Examples
Embodiment Construction
[0021] The present invention will be further described below in conjunction with the embodiments shown in the accompanying drawings.
[0022] The main problem to be solved by the invention is to effectively suppress the lateral vibration of the cables, especially the long cables. The invention relates to a novel method and device for active variable stiffness control of cable vibration.
[0023] 1) The new method of active variable stiffness control of cable vibration is the D-V-I Bang-Bang control strategy for the multi-order modal vibration response of the cable, that is, the Bang-Bang control strategy based on the displacement-velocity product integral. The specific expression is as follows:
[0024] U ( t ) = k ∫ 0 l v ...
PUM
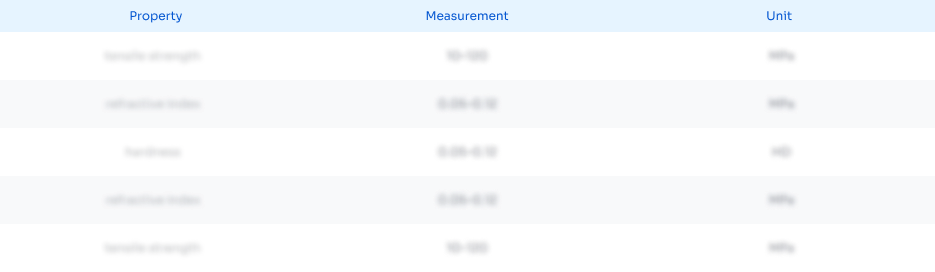
Abstract
Description
Claims
Application Information

- Generate Ideas
- Intellectual Property
- Life Sciences
- Materials
- Tech Scout
- Unparalleled Data Quality
- Higher Quality Content
- 60% Fewer Hallucinations
Browse by: Latest US Patents, China's latest patents, Technical Efficacy Thesaurus, Application Domain, Technology Topic, Popular Technical Reports.
© 2025 PatSnap. All rights reserved.Legal|Privacy policy|Modern Slavery Act Transparency Statement|Sitemap|About US| Contact US: help@patsnap.com