Material mixer used for high temperature difference quick reaction
A fast-response, material-mixing technology, applied in the direction of single-component polyamide rayon, etc., can solve problems such as easy sticking to the mixer wall, difficulty in flowing, and low molecular weight of the resin
- Summary
- Abstract
- Description
- Claims
- Application Information
AI Technical Summary
Problems solved by technology
Method used
Image
Examples
Embodiment 1
[0034] This example refers to the solvent NMP-CaCl 2 In the process of producing poly(p-phenylene terephthalamide) resin, the two polymerization reactors in this process are twin-screw reactors.
[0035] Dissolved in NMP-CaCl 2 It contains 4.5% to 8% p-phenylenediamine, cool it to the required temperature, add part of the prepolymer A solution generated by the reaction of terephthaloyl chloride (accounting for 20% to 50% of the total), the prepolymer Cool to 0℃~15℃ for later use, meanwhile, heat and melt B material terephthaloyl chloride, and control the temperature at 85℃~120℃. After the preparation work, the two materials should be sprayed with the stoichiometric coefficient as the ratio. In the mixer, violent collision mixing is carried out at the middle position of the mixing chamber to generate a relatively dilute (viscosity within 100cp) mixture that enters the first polymerization reactor after staying in the mixer for about 1 second (the mixer piston is 2 to 5 times / ...
PUM
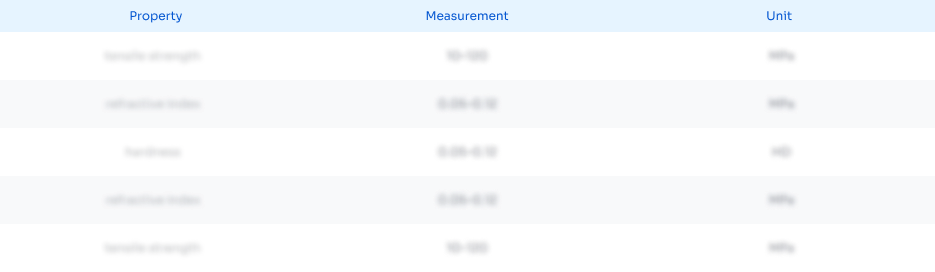
Abstract
Description
Claims
Application Information

- Generate Ideas
- Intellectual Property
- Life Sciences
- Materials
- Tech Scout
- Unparalleled Data Quality
- Higher Quality Content
- 60% Fewer Hallucinations
Browse by: Latest US Patents, China's latest patents, Technical Efficacy Thesaurus, Application Domain, Technology Topic, Popular Technical Reports.
© 2025 PatSnap. All rights reserved.Legal|Privacy policy|Modern Slavery Act Transparency Statement|Sitemap|About US| Contact US: help@patsnap.com