Passive hydraulic control linked error correcting machine
A technology of deviation correction machine and passive fluid, which is applied in the field of deviation correction devices, and can solve problems such as high failure rate, poor working environment, and insufficient correction force
- Summary
- Abstract
- Description
- Claims
- Application Information
AI Technical Summary
Problems solved by technology
Method used
Image
Examples
Embodiment Construction
[0019] The present invention will be further described below in conjunction with the accompanying drawings.
[0020] The belt (12) is placed on the idler roller (11) of the passive hydraulic control linkage self-correcting machine. The inspection drive wheel (1) oil pump (2) is between the idler on the driving idler bracket (8) and the idler on the driven idler bracket (10), on both sides of the edge of the belt (1). The thermostat (13) is higher than the level of the oil pump (2) and is installed on the frame (14). The central control station (6) is fixed on the frame (14). The cylinder body of the oil cylinder (4) is hinged with the frame (14), and the end of the piston rod is hinged with the end of the active arm rod (5).
[0021] Each oil port of the oil pump (2), oil cylinder (4), and thermostat (12) is connected to the central control station (3) through oil pipes.
[0022] When the belt (12) runs off-center, the edge of the belt (12) touches the detection drive wheel...
PUM
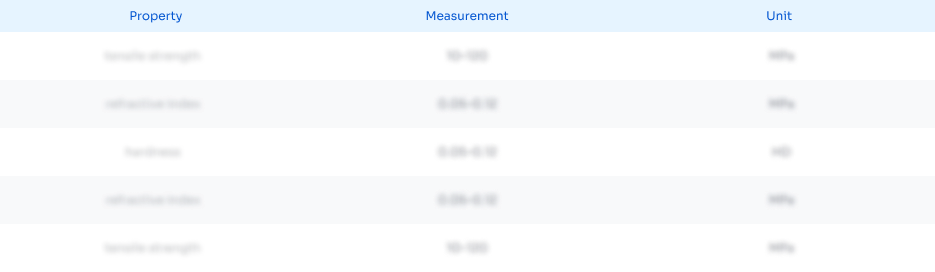
Abstract
Description
Claims
Application Information

- Generate Ideas
- Intellectual Property
- Life Sciences
- Materials
- Tech Scout
- Unparalleled Data Quality
- Higher Quality Content
- 60% Fewer Hallucinations
Browse by: Latest US Patents, China's latest patents, Technical Efficacy Thesaurus, Application Domain, Technology Topic, Popular Technical Reports.
© 2025 PatSnap. All rights reserved.Legal|Privacy policy|Modern Slavery Act Transparency Statement|Sitemap|About US| Contact US: help@patsnap.com