Alkaline method for zero-residual alkaline boiling pulp making method
A technology for pulping and residual alkali, applied in the field of papermaking and pulping, can solve the problems of high operating costs and large investment in alkali recovery technology, and achieve the effects of saving production costs, high cooking efficiency and high calorific value.
- Summary
- Abstract
- Description
- Claims
- Application Information
AI Technical Summary
Problems solved by technology
Method used
Examples
Embodiment 1
[0029] To 1000g of broken and dust-removed reeds, add 300ml of alkali solution with a temperature of 80°C and a concentration of 5%. After fully stirring, keep warm and pre-soak for 2 hours, then remove the free alkali solution, add catalyst A, stir evenly, and then add Cook in a cooking pot. The cooking pressure is 1.3-1.5Mpa, the cooking time is 10-30min, the slurry concentration is 20-25%, the pH value of the slurry is 6.5-7.5, the pH value of the black liquor is 6.5-7.5, and the mass dosage of catalyst A is 2%. : Sodium sulfite 1.6%, magnesium hydroxide and sodium silicate 0.2% each. Afterwards, the refining and papermaking process is the same as the conventional process. The beating degree of pulping is 38 degrees. It is mixed with domestic waste paper pulp to make high-strength corrugated base paper. The proportion of reed pulp is 20% (mass ratio). Meet the standard of GB13023-91A grade corrugated base paper.
Embodiment 2
[0031] In 1000g of broken and dust-removed cotton stalks, add 300ml of alkali solution with a temperature of 80°C and a concentration of 4%. After fully stirring, keep warm and pre-soak for 4 hours, then remove free alkali, add catalyst A, stir evenly, and then Add to cooking pot to cook. The cooking pressure is 1.2-1.4Mpa, the cooking time is 30-60min, the slurry concentration is 20-25%, the pH value of the slurry is 6.5-7.5, the pH value of the black liquor is 6.5-7.5, and the mass dosage of catalyst A is 4%. Anthraquinone 0.1%, sodium sulfite 3.5%, potassium hydroxide 0.3% and urea 0.1%. The pulping and papermaking part is the same as the conventional process, the beating degree of pulping is 35 degrees, and the high-strength corrugated base paper is blended with domestic waste paper pulp, and the proportion of cotton straw pulp is 30%, and the quality indicators of the finished paper all reach GB13023-91A level Standard for corrugated base paper.
Embodiment 3
[0033] Add 300ml of alkali solution with a temperature of 80°C and a concentration of 6% to 1000g of broken and dedusted bamboo chips, stir well, keep warm and pre-soak for 5 hours, then remove free alkali, add catalysts A and B, and stir evenly , and then added to the cooking pot for cooking. The cooking pressure is 1.0-1.3Mpa, the cooking time is 60-90min, the slurry concentration is 20-25%, the pH value of the slurry is 6.5-7.5, the pH value of the black liquor is 6.5-7.5, and the mass dosage of catalyst A is 3%. : 0.15% of anthraquinone, 2.7% of sodium sulfite and 0.15% of magnesium hydroxide, the mass consumption of catalyst B is 2.5%, wherein: 2% of hydrogen peroxide, 0.5% of sulfamic acid. The refining and papermaking process is the same as the conventional process. The beating degree of pulping is 42 degrees. After beating, 80g kraft paper is produced. The quality indicators of the finished paper all meet the requirements of QB / T3516-1999 standard A-grade paper.
PUM
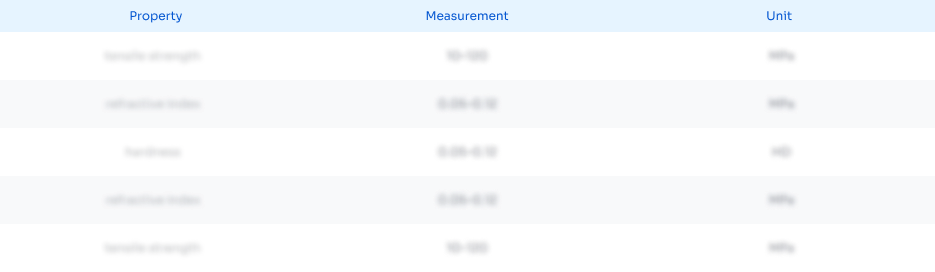
Abstract
Description
Claims
Application Information

- Generate Ideas
- Intellectual Property
- Life Sciences
- Materials
- Tech Scout
- Unparalleled Data Quality
- Higher Quality Content
- 60% Fewer Hallucinations
Browse by: Latest US Patents, China's latest patents, Technical Efficacy Thesaurus, Application Domain, Technology Topic, Popular Technical Reports.
© 2025 PatSnap. All rights reserved.Legal|Privacy policy|Modern Slavery Act Transparency Statement|Sitemap|About US| Contact US: help@patsnap.com