MnZn ferrite material and method of manufacturing the magnetic core
A manufacturing method, soft ferrite technology, applied in the direction of inorganic material magnetism, inductance/transformer/magnet manufacturing, electrical components, etc., can solve the problems of current rise, burn-in, coil heating, etc., and achieve the effect of low power loss
- Summary
- Abstract
- Description
- Claims
- Application Information
AI Technical Summary
Problems solved by technology
Method used
Examples
Embodiment 1
[0027] According to iron oxide Fe 2 o 3 : manganese oxide MnO: zinc oxide ZnO=52.2: 37.6: 10.2mol% of the formula for a batching, wherein manganese oxide Fe 2 o 3 Purity ≥ 99.3wt%, manganese oxide MnO purity ≥ 98.8wt%, zinc oxide ZnO purity ≥ 99.7wt%, pour the three raw materials into a mixing tank, add a conventional amount of dispersant and deionized water, and fully stir and mix , and ball milled for 3 hours; conventional spray drying was carried out, and then pre-calcined, the pre-fired temperature was 800°C, and the pre-fired time was 80 minutes, and the calcined material was obtained; the calcined material was put into a ball mill for secondary batching, and the following 500ppm by weight of silicon dioxide SiO 2 and 1000 ppm by weight of bismuth trioxide Bi 2 o 3 Add conventional amount of deionized water, dispersant and defoamer, and ball mill for 3 hours to obtain black slurry; pour the slurry into the mixing tank, and then carry out conventional spray granulatio...
Embodiment 2
[0029] According to iron oxide Fe 2 o 3 : manganese oxide MnO: zinc oxide ZnO=52: 37.8: 9.88mol% of the formula for a batching, wherein iron oxide Fe 2 o 3Purity ≥ 99.3wt%, manganese oxide MnO purity ≥ 98.8wt%, zinc oxide ZnO purity ≥ 99.7wt%, pour the three raw materials into a mixing tank, add a conventional amount of dispersant and deionized water, and fully stir and mix uniform, ball milling for 4 hours; conventional spray drying, and pre-burning, the pre-burning temperature was 840 ° C, and the pre-burning time was 70 minutes, and the calcined material was obtained; the calcined material was put into a ball mill for secondary batching, and Add 400ppm by weight of the first subcomponent tantalum pentoxide Ta 2 o 5 and 1500ppm by weight of the second subcomponent niobium pentoxide Nb 2 o 5 , add a conventional amount of deionized water, dispersant and defoamer, and ball mill for 4 hours to obtain a black slurry; pump the slurry into the mixing tank, and then spray gra...
Embodiment 3
[0031] According to iron oxide Fe 2 o 3 : manganese oxide MnO: zinc oxide ZnO=51.8: 37.4: 10.8mol% of the formula for a batching, wherein iron oxide Fe 2 o 3 Purity ≥ 99.3wt%, manganese oxide MnO purity ≥ 98.8wt%, zinc oxide ZnO purity ≥ 99.7wt%, pour the three raw materials into a mixing tank, add a conventional amount of dispersant and deionized water, and fully stir and mix uniform, ball milling for 5 hours; conventional spray drying, and then pre-burning, the pre-burning temperature is 900 ° C, and the pre-burning time is 50 minutes, and the calcined material is obtained; the calcined material is put into the ball mill for secondary batching, and Add 600ppm by weight of the first subcomponent silicon dioxide SiO 2 , tantalum pentoxide Ta 2 o 5 Mixture and 2000ppm by weight of the second subcomponent bismuth trioxide Bi 2 o 3 , Tungsten trioxide WO 3 Add a conventional amount of deionized water, dispersant and defoamer to the mixture, and ball mill for 3 hours to ob...
PUM
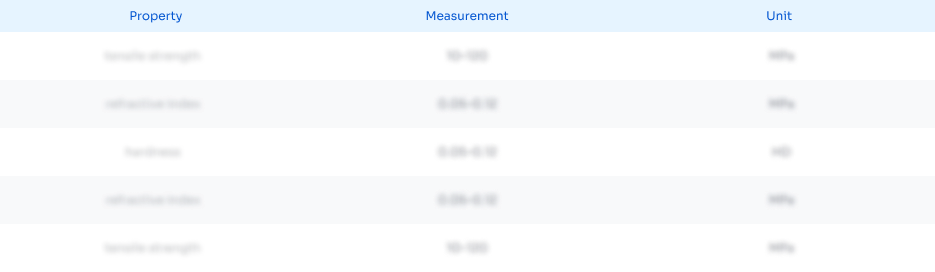
Abstract
Description
Claims
Application Information

- R&D
- Intellectual Property
- Life Sciences
- Materials
- Tech Scout
- Unparalleled Data Quality
- Higher Quality Content
- 60% Fewer Hallucinations
Browse by: Latest US Patents, China's latest patents, Technical Efficacy Thesaurus, Application Domain, Technology Topic, Popular Technical Reports.
© 2025 PatSnap. All rights reserved.Legal|Privacy policy|Modern Slavery Act Transparency Statement|Sitemap|About US| Contact US: help@patsnap.com