Compounded oil phase for powder nitramon
A technology of ammonium nitrate explosives and composite oil phase, which is applied in the direction of explosives, etc., can solve the problems of complex production process, high production cost, and large investment in equipment, and achieve the effects of high combustion calorific value, low cost, and improved detonation sensitivity
- Summary
- Abstract
- Description
- Claims
- Application Information
AI Technical Summary
Problems solved by technology
Method used
Examples
Embodiment 1
[0027] Composite oil phase for powdery ammonium nitrate explosives, including the following raw materials in parts by weight: 76 parts of paraffin, 20 parts of diesel oil, 2.0 parts of dinitromethane, 2.0 parts of β-naphthalenesulfonate calcium salt and formaldehyde condensation product;
[0028] Get above-mentioned components, make the composite oily phase that contains nitromethane of the present invention with following preparation steps:
[0029] a. After melting the paraffin wax at a temperature of 75-85°C, adding diesel oil for mixing and melting to obtain a fuel oil mixture;
[0030] b. Turn on the agitator under normal pressure, slowly add β-naphthalene sulfonate calcium salt and formaldehyde condensate to the fuel oil mixture, mix for 5 minutes, and the temperature is 75-85°C to form a modified oil phase;
[0031] c. Slowly add dinitromethane into the modified oil phase and mix for 5 minutes at a temperature of 75-85°C to form a composite oil phase containing nitromet...
Embodiment 2
[0033] Composite oil phase for powdery ammonium nitrate explosives, including the following raw materials in parts by weight: 72 parts of asphalt, 20 parts of diesel oil, 5.0 parts of mononitromethane, 3.0 parts of β-naphthalenesulfonate calcium salt and formaldehyde condensation product;
[0034] Get above-mentioned components, make the composite oily phase that contains nitromethane of the present invention with following preparation steps:
[0035] a. After melting the asphalt at a temperature of 80-90°C, adding diesel oil and mixing it to obtain a fuel oil mixture;
[0036] b. Turn on the agitator under normal pressure, slowly add β-naphthalene sulfonate calcium salt and formaldehyde condensate to the fuel oil mixture, mix for 10 minutes, and the temperature is 80-90°C to form a modified oil phase;
[0037] c. Slowly add mononitromethane into the modified oil phase and mix for 10 minutes at a temperature of 80-90°C to form a composite oil phase containing nitromethane.
Embodiment 3
[0039] Composite oil phase for powdery ammonium nitrate explosives, including the following raw materials in parts by weight: 66 parts of paraffin, 10 parts of rosin, 15 parts of diesel oil, 5.0 parts of engine oil, 3.0 parts of dinitromethane, β naphthalene sulfonate magnesium formaldehyde condensation 1.0 parts;
[0040] Get above-mentioned components, make the composite oily phase that contains nitromethane of the present invention with following preparation steps:
[0041] a. After melting paraffin and rosin at a temperature of 85-95°C, add diesel oil and engine oil to mix and melt to obtain a fuel oil mixture;
[0042] b. Turn on the agitator under normal pressure, slowly add β-naphthalenesulfonic acid sodium salt and formaldehyde condensate to the fuel oil mixture, mix for 8 minutes, and the temperature is 85-95°C to form a modified oil phase;
[0043] c. Slowly add dinitromethane into the modified oil phase and mix for 8 minutes at a temperature of 85-95°C to form a co...
PUM
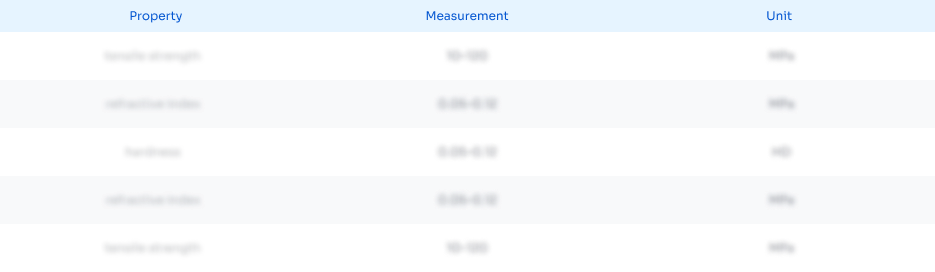
Abstract
Description
Claims
Application Information

- R&D
- Intellectual Property
- Life Sciences
- Materials
- Tech Scout
- Unparalleled Data Quality
- Higher Quality Content
- 60% Fewer Hallucinations
Browse by: Latest US Patents, China's latest patents, Technical Efficacy Thesaurus, Application Domain, Technology Topic, Popular Technical Reports.
© 2025 PatSnap. All rights reserved.Legal|Privacy policy|Modern Slavery Act Transparency Statement|Sitemap|About US| Contact US: help@patsnap.com