Reactive dyestuff dyeing and fixing technique and printing and dyeing auxiliary agent used for the same
A technology of reactive dyes and printing and dyeing auxiliaries, which can be used in dyeing, textiles and papermaking, and can solve the problems of large amount of alkaline color fixing agent and low cost
- Summary
- Abstract
- Description
- Claims
- Application Information
AI Technical Summary
Problems solved by technology
Method used
Examples
example 1
[0084] Example 1 Normal temperature and pressure dyeing of a certain type of cotton knitted fabric
[0085]In the old-fashioned 4-tube normal temperature and pressure dyeing machine with a volume of 400Kg produced by Taiwan Tobu Seiki Co., Ltd. in 1996, 286Kg of pre-treated 32s cotton knitted jersey was worn; water was added and the car was driven; the pre-weighed Add 18Kg of black dye made of red, yellow and blue certain type of double active group reactive dyes of a certain company into the chemical material tank, homogenize with an appropriate amount of hot water, and add it to the dyeing machine at one time; after 10 minutes, put 150Kg of sodium sulfate in the chemical Melt water in the material vat and add it to the vat; run for 10 minutes; directly raise the temperature to 60°C, add 7.5Kg of Shanghai Xinfa High-tech Co., Ltd. high-efficiency active dyeing and fixing one-bath accelerator SBS-169 into the dyeing vat at one time, and keep the temperature constant After 80 m...
example 2
[0087] Example 2 Extend the effect of a commercially available liquid color-fixing alkali SH from one to two
[0088] With reference to the method of example 1, the dyestuff can be changed into a certain color 17.4Kg composed of a certain type of reactive dye of any company, red, yellow and blue. 160Kg; dyeing a certain type of knitted fabric 300Kg; the dyeing depth is consistent with the sample. Compared with the original use of color-fixing alkali (or substitute alkali) SH, it saves 300Kg more sodium sulfate, saves nearly one ton of steam, and more than 5 tons of water; One, expanded to be used in two functions of greatly reducing the amount of salt used as a dyeing accelerator at the same time. The extended usage of Example 1 is applicable to this example.
example 3
[0089] Example 3 High temperature and high pressure dyeing of a certain type of knitted fabric
[0090] Use a certain type of high temperature and high pressure jet dyeing machine to dye 500Kg of a certain type of knitted fabric that has been pretreated. The dye is a certain type of reactive 3B red from a certain company, with a dosage of 6%, and 150Kg of sodium sulfate; after the cloth is threaded, add water, Cover and pressurize to a gauge pressure of 0.1Mpa; other reference example 1; after the dyeing time is in place, release the pressure; take a sample. But after soaping, wash with hot water 3 to 4 times, and wash with cold water 2 to 3 times. The depth is reached; the soap boiling fastness is 4.5-5 grades. By adopting this method, more than 50% of sodium sulfate, about 140-160Kg, and 10% of dyestuffs can be saved compared with the conventional process. In addition, soda ash is completely abandoned, one soap boil and three to four water washes are omitted, saving more t...
PUM
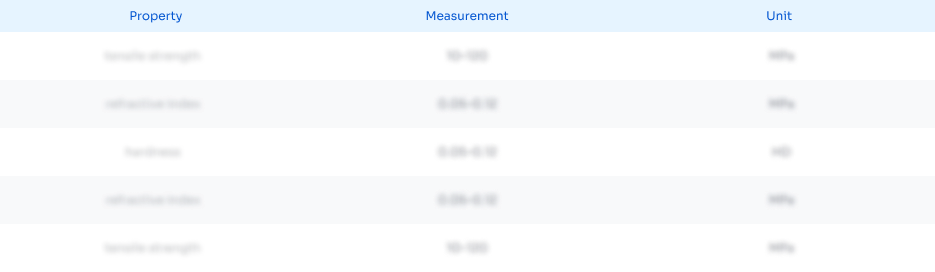
Abstract
Description
Claims
Application Information

- R&D
- Intellectual Property
- Life Sciences
- Materials
- Tech Scout
- Unparalleled Data Quality
- Higher Quality Content
- 60% Fewer Hallucinations
Browse by: Latest US Patents, China's latest patents, Technical Efficacy Thesaurus, Application Domain, Technology Topic, Popular Technical Reports.
© 2025 PatSnap. All rights reserved.Legal|Privacy policy|Modern Slavery Act Transparency Statement|Sitemap|About US| Contact US: help@patsnap.com