Technique for producing peach gum powder
A production process and technology of peach gum powder, applied in the field of production and processing technology of peach gum powder, can solve the problems of low extraction rate and extraction purity, unreasonable process route, simple process flow, etc., and save time and effort in the processing process. , the process route is reasonable, the effect of high purity
- Summary
- Abstract
- Description
- Claims
- Application Information
AI Technical Summary
Problems solved by technology
Method used
Examples
Embodiment 1
[0024] (1) Soaking to remove impurities
[0025] Rinse the peach gum with clean water to remove impurities such as silt and bark, soak the peach gum evenly and grind it with a pulverizer;
[0026] (2) Hydrolysis
[0027] Put the crushed peach gum and water into the reaction kettle at a ratio of 1:8, add the peach gum protective agent, add the degradation agent when the material is stirred evenly and the temperature rises to 50°C, continue to heat up, and keep the temperature for 8 hours after the temperature reaches 90°C , to obtain peach collagen solution;
[0028] (3) clarification and decolorization
[0029] The peach collagen solution is directly pumped from the reaction kettle to the clarification tank for clarification. Because colored substances are easily produced during hydrolysis, a decolorizing agent is added for decolorization treatment. After 30 hours of precipitation and clarification, the clarified glue is obtained.
[0030] (4) centrifugal impurity removal ...
Embodiment 2
[0041] (1) Soaking to remove impurities
[0042] Rinse the peach gum with clean water to remove impurities such as silt and bark, soak the peach gum evenly and then grind it;
[0043] (2) Hydrolysis
[0044] Put the crushed peach gum and water into the reaction kettle at a ratio of 1:9, add peach gum protective agent, add degradation agent when the material is stirred evenly and the temperature rises to 55°C, continue to heat up, and keep the temperature for 10 hours after the temperature reaches 95°C , to obtain peach collagen solution;
[0045] (3) clarification and decolorization
[0046] The peach collagen solution is directly pumped from the reaction kettle to the clarification tank for clarification. Because colored substances are easily produced during hydrolysis, a decolorizing agent is added for decolorization treatment. After 36 hours of precipitation and clarification, the clarified glue is obtained.
[0047] (4) centrifugal impurity removal
[0048] The clarifi...
Embodiment 3
[0058] (1) Soaking to remove impurities
[0059] Rinse the peach gum with clean water to remove impurities such as silt and bark, soak the peach gum evenly and then grind it;
[0060] (2) Hydrolysis
[0061] Put the crushed peach gum and water into the reaction kettle at a ratio of 1:7, add the peach gum protective agent, add the degradation agent when the material is stirred evenly and the temperature rises to 45°C, continue to heat up, and keep the temperature for 6 hours after the temperature reaches 85°C , to obtain peach collagen solution;
[0062] (3) clarification and decolorization
[0063] The peach collagen solution is directly pumped from the reaction kettle to the clarification tank for clarification. Because colored substances are easily produced during hydrolysis, a decolorizing agent is added for decolorization treatment. After 24 hours of precipitation and clarification, the clarified glue solution is obtained.
[0064] (4) centrifugal impurity removal
[0...
PUM
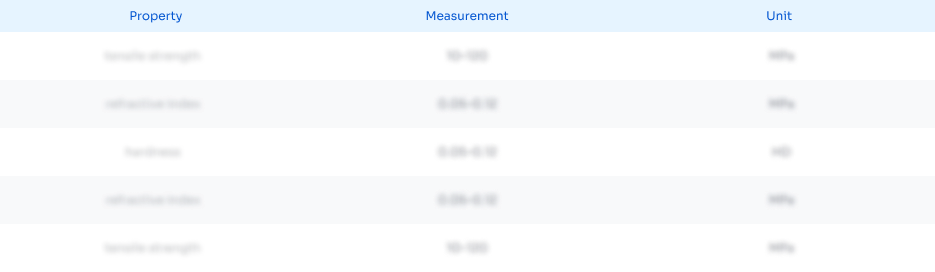
Abstract
Description
Claims
Application Information

- Generate Ideas
- Intellectual Property
- Life Sciences
- Materials
- Tech Scout
- Unparalleled Data Quality
- Higher Quality Content
- 60% Fewer Hallucinations
Browse by: Latest US Patents, China's latest patents, Technical Efficacy Thesaurus, Application Domain, Technology Topic, Popular Technical Reports.
© 2025 PatSnap. All rights reserved.Legal|Privacy policy|Modern Slavery Act Transparency Statement|Sitemap|About US| Contact US: help@patsnap.com