Heating spiral rod for processing plastic machine and its manufacturing method
A technology of heating screw and manufacturing method, applied in the field of heating screw for processing plastic machines, can solve the problems of immature structure, waste of heat energy, damage to high-temperature wires of porcelain rods, etc., and achieve convenient installation and replacement, reduce production costs, and reduce maintenance. cost effect
- Summary
- Abstract
- Description
- Claims
- Application Information
AI Technical Summary
Problems solved by technology
Method used
Image
Examples
Embodiment 2
[0024] Embodiment 2 of the present invention: make hollow screw rod 1, machine pipe 11 is installed outside screw rod 1, put into 20 sections of porous refractory bricks 4 in screw rod 1, each porous refractory bricks 4 are connected in a row, on porous refractory bricks 4 A heating hole 5 is provided, and the heating hole 5 penetrates to form the long hole 3 . Make a positioning hole 6 in the middle of the porous refractory brick 4, penetrate the positioning shaft 7 in the positioning hole 6, put a plurality of porous refractory bricks 4 on the positioning shaft 7, and then the porous refractory brick 4 can be fixed. The cross sections of the positioning hole 6 and the positioning shaft 7 are regular hexagons.
[0025] Make 6 centrally symmetrical heating holes 5 on the porous refractory brick 4 . Porous refractory brick 4 is made into cylindrical shape, and length is 6 centimetres.
[0026] The heating element 2 adopts an electric furnace wire 8, and the connecting head of...
PUM
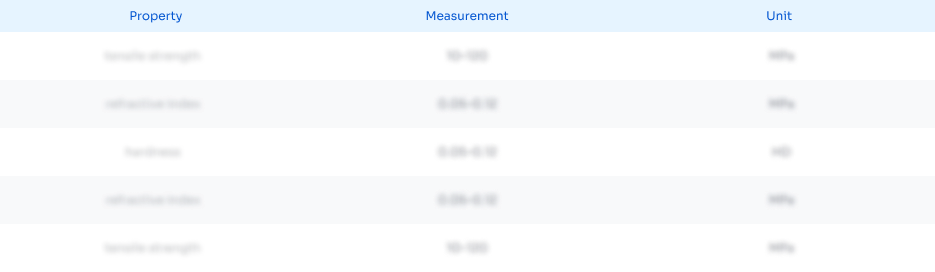
Abstract
Description
Claims
Application Information

- R&D
- Intellectual Property
- Life Sciences
- Materials
- Tech Scout
- Unparalleled Data Quality
- Higher Quality Content
- 60% Fewer Hallucinations
Browse by: Latest US Patents, China's latest patents, Technical Efficacy Thesaurus, Application Domain, Technology Topic, Popular Technical Reports.
© 2025 PatSnap. All rights reserved.Legal|Privacy policy|Modern Slavery Act Transparency Statement|Sitemap|About US| Contact US: help@patsnap.com