Method for separating phenols compounds from phenol-containing raw material oil
A technology of phenolic compounds and raw oil, which is applied in the preparation of organic compounds, chemical instruments and methods, organic chemistry, etc., can solve the problems of serious corrosion, complexity, and high energy consumption of equipment, and reduce sewage discharge, improve the environment, The effect of low energy consumption
- Summary
- Abstract
- Description
- Claims
- Application Information
AI Technical Summary
Problems solved by technology
Method used
Examples
Embodiment 2
[0023] Mix 100 g of raw material 2 with saturated ammonia solution, the volume ratio of oil agent is 1:5, the reaction temperature is 35° C., and the contact time is 25 minutes to separate the two phases. The obtained aqueous ammonium salt solution containing phenolic compounds was passed through carbon dioxide at 25° C., the ammonium salts of phenolic compounds were decomposed, and phenolic compounds, ie crude phenol, were liberated. The yield of crude phenol was 95%. Carbon dioxide with ammonia and NH 4 + Form NH 4 HCO 3 , stop feeding carbon dioxide when the pH value reaches 6.5. Will NH 4 HCO 3 The aqueous solution is heated to 85°C, NH 4 HCO 3 Decompose into ammonia and carbon dioxide gas, ammonia dissolves in water, carbon dioxide is discharged, when the pH value of the solution reaches 10, stop heating. Carbon dioxide and ammonia are recycled.
Embodiment 3
[0025] According to Example 1, use saturated ammonia water with a weight concentration of 10% ammonia solution, the volume ratio of the raw material to the ammonia solution is 1:6, and react at 25°C for 20 minutes, and the phenolic compound in the raw material reacts with ammonia to generate ammonium salt , separated from the raw material, dissolved in ammonia solution, and separated the oil phase and the water phase. Then, at the same temperature, carbon dioxide gas is passed into the water phase, and the ammonium salt of the phenolic compound is decomposed, and the phenolic compound, that is, crude phenol, is released, and the yield reaches 95%. Carbon dioxide with ammonia and NH 4 + Form NH 4 HCO 3 , stop feeding carbon dioxide when the pH value reaches 7. Heat the aqueous phase to 75°C, NH 4 HCO 3 Decompose into ammonia and carbon dioxide gas, ammonia dissolves in water, carbon dioxide is discharged, when the pH value of the solution reaches 11, stop heating. Carbon...
Embodiment 4
[0027] According to embodiment 3, ammonia solution is 25wt%, and the volume ratio of raw material and ammonia solution is 1: 3, and reaction temperature is 15 ℃, and the reaction time is 30 minutes, and the phenolic compound in the raw material reacts with ammonia to generate ammonium salt, from raw material Come out, dissolve in ammonia solution, and separate the oil and water phases. Then, at the same temperature, the ammonium salt of the phenolic compound is decomposed into the water phase with carbon dioxide gas, and the phenolic compound, namely crude phenol, is released, and the yield reaches 96%. Carbon dioxide with ammonia and NH 4 + Form NH 4 HCO 3 . When the pH value reached 6.5, stop feeding carbon dioxide. Heat the aqueous phase to 65°C, NH 4 HCO 3 Decompose into ammonia and carbon dioxide gas, ammonia dissolves in water, carbon dioxide is discharged, when the pH value of the solution reaches 10, stop heating. Carbon dioxide and ammonia are recycled.
PUM
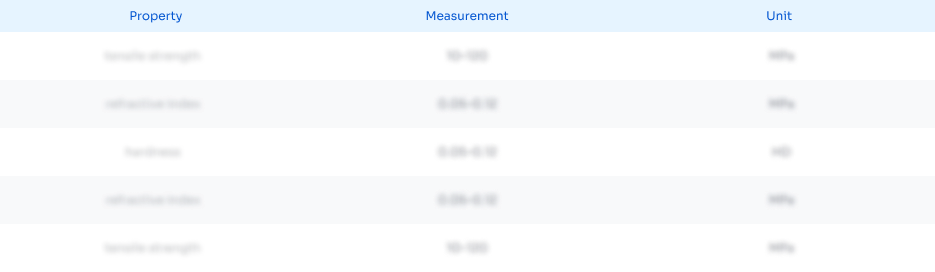
Abstract
Description
Claims
Application Information

- R&D
- Intellectual Property
- Life Sciences
- Materials
- Tech Scout
- Unparalleled Data Quality
- Higher Quality Content
- 60% Fewer Hallucinations
Browse by: Latest US Patents, China's latest patents, Technical Efficacy Thesaurus, Application Domain, Technology Topic, Popular Technical Reports.
© 2025 PatSnap. All rights reserved.Legal|Privacy policy|Modern Slavery Act Transparency Statement|Sitemap|About US| Contact US: help@patsnap.com