Oxygen-sulfur paragenesis zinc mine flotation method
A zinc ore, oxygen-sulfur technology, applied in flotation, solid separation and other directions, can solve the problems of high production cost, waste of resources, low recovery rate of zinc oxide flotation, etc., to solve high cost, save cost, and improve resource integration The effect of utilization
- Summary
- Abstract
- Description
- Claims
- Application Information
AI Technical Summary
Problems solved by technology
Method used
Examples
Embodiment 1
[0021] 1. Mineral raw materials: a mixed ore with a raw ore zinc grade of 5.4% and an oxidation rate of 60% in a concentrator in Guizhou.
[0022] 2. Flotation process: 1 roughing, 3 fine selections, 4 sweeps.
[0023] 3. Chemical system: sodium hexametaphosphate 200g / t, sodium sulfide 5kg / t, octadecyl ammonium acetate 250g / t, kerosene 100g / t, No. 2 oil 70g / t.
[0024] When in use, it is first formulated into the following concentrations (% by weight):
[0025] Sodium hexametaphosphate 5% aqueous solution
[0026] Sodium sulfide 20% aqueous solution
[0027] Ammonium Octadecyl Acetate 20% Emulsion
[0028] Kerosene direct dope addition
[0029] No. 2 oil, direct stock solution addition
[0030] 4. Flotation index: Zinc recovery rate reaches 86%, concentrate grade is 39.8%, tailings zinc content is 0.55%, among which zinc sulfide part reaches 90%.
Embodiment 2
[0032] 1. Mineral raw materials: a mixed ore with a zinc grade of 1.7% and an oxidation rate of 20% in a dressing plant in Hunan.
[0033] 2. Flotation process: 1 time of rough selection, 3 times of fine selection, 4 times of sweeping.
[0034] 3. Chemical system: first use 3kg / t sodium sulfide to mix the pulp, then add 200g / t octadecyl amine acetate, 100g / t kerosene, and 60g / t No. 2 oil.
[0035] When in use, it is first formulated to the following concentrations (% by weight):
[0036] Sodium hexametaphosphate 1% aqueous solution
[0037] Sodium sulfide 10% aqueous solution
[0038] Ammonium Octadecyl Acetate 5% Emulsion
[0039] Kerosene direct dope addition
[0040] No. 2 oil, direct stock solution addition
[0041] 4. Flotation index: Zinc recovery rate reaches 91%, concentrate grade is 51.25%, tailings zinc content is 0.14%.
PUM
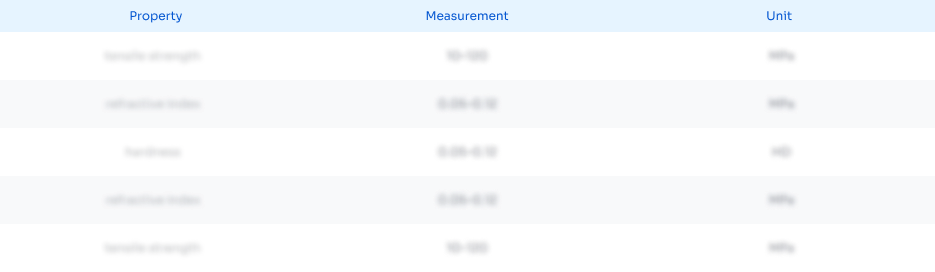
Abstract
Description
Claims
Application Information

- R&D
- Intellectual Property
- Life Sciences
- Materials
- Tech Scout
- Unparalleled Data Quality
- Higher Quality Content
- 60% Fewer Hallucinations
Browse by: Latest US Patents, China's latest patents, Technical Efficacy Thesaurus, Application Domain, Technology Topic, Popular Technical Reports.
© 2025 PatSnap. All rights reserved.Legal|Privacy policy|Modern Slavery Act Transparency Statement|Sitemap|About US| Contact US: help@patsnap.com