Spherical tooth type universal coupling
A universal coupling and semi-coupling technology, applied in the direction of couplings, elastic couplings, mechanical equipment, etc., can solve problems such as poor sealing and lubrication, limited torque transmission, and unstable angular velocity, etc., to achieve The effect of large torque transmission, reduced contact stress, and increased force-bearing contact area
- Summary
- Abstract
- Description
- Claims
- Application Information
AI Technical Summary
Problems solved by technology
Method used
Image
Examples
Embodiment Construction
[0014] In the embodiment shown in the accompanying drawings, the spherical tooth type universal coupling of the present invention has a symmetrical structure at both left and right ends. It includes an intermediate coupling shaft 1, and the two ends of the intermediate coupling shaft 1 are respectively processed with hemispherical spherical grooves 9, and the end caps 2 and 3 connected to the two ends of the intermediate coupling shaft 1 are respectively installed in the spherical groove 9. Half-couplings, the said half-couplings are spherical ball joints 4 and 5 connected to the power input end 6 and the power output end 7 respectively, and the front hemispherical surfaces of the ball joints 4 and 5 are evenly processed. The convex arc-shaped teeth 8 are processed in the spherical groove 9 with the concave arc-shaped teeth 10 meshing with the convex arc-shaped teeth 8 on the ball joints 4 and 5, and the combination transmits torque. The inner cavities of the end caps 2 and 3 ...
PUM
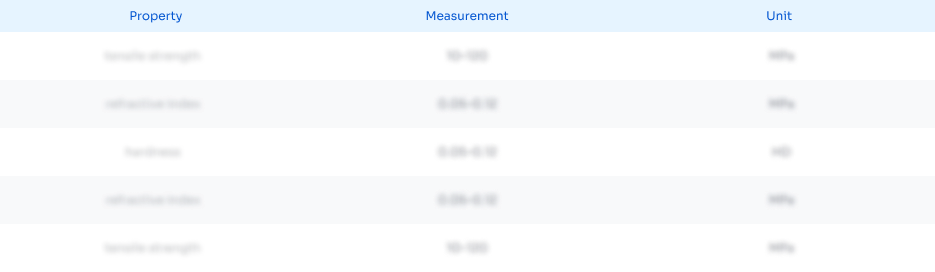
Abstract
Description
Claims
Application Information

- R&D Engineer
- R&D Manager
- IP Professional
- Industry Leading Data Capabilities
- Powerful AI technology
- Patent DNA Extraction
Browse by: Latest US Patents, China's latest patents, Technical Efficacy Thesaurus, Application Domain, Technology Topic, Popular Technical Reports.
© 2024 PatSnap. All rights reserved.Legal|Privacy policy|Modern Slavery Act Transparency Statement|Sitemap|About US| Contact US: help@patsnap.com