Two-sided polishing method for gallium phosphide crystal plate
A double-sided polishing and gallium phosphide technology, which is applied to surface polishing machine tools, grinding/polishing equipment, electrical components, etc., can solve the problems that there is no publication of double-sided polishing methods for gallium phosphide (111) wafers, etc. The method is simple, practical and operable
- Summary
- Abstract
- Description
- Claims
- Application Information
AI Technical Summary
Problems solved by technology
Method used
Examples
Embodiment 1
[0015] (1) Prepare a cleaning solution with a concentration of 15%, heat it to 50°C, and then put the flower basket containing the wafer into ultrasonic cleaning for 10 minutes, and rinse thoroughly;
[0016] (2) Mounting is carried out when the surface temperature of the polishing disc is 40°C;
[0017] (3) Prepare a polishing solution (FUJIMI INSEC P powder:pure water 1:10), and perform ultrasonication for 30 minutes; set the pressure of the polishing machine to 10 psi, and the flow rate of the polishing solution to 40 ml / min for polishing.
[0018] (4) After the reverse side is polished, other conditions remain unchanged. The polishing pressure value is set to 20psi, and the flow rate of the polishing liquid is 30ml / min.
[0019] (5) Ultrasonic cleaning in a cleaning solution with a concentration of 20% and a temperature of 70°C for 20 minutes, fully flushed, then corroded in 80°C hot acid for 2 minutes, and soaked in cold alkali for 1 minute.
[0020] Experimental results...
Embodiment 2
[0022] (1) Prepare a cleaning solution with a concentration of 20%, heat it to 50°C, and then put the flower basket containing the wafer into ultrasonic cleaning for 10 minutes, and rinse thoroughly;
[0023] (2) Mounting is carried out when the surface temperature of the polishing disc is 40°C;
[0024] (3) Prepare a polishing liquid (FUJIMI INSEC P powder:pure water 3:20), and ultrasonicate for 30 minutes; set the pressure value of the polishing machine to 30 psi, and the flow rate of the polishing liquid to 10 ml / min for polishing.
[0025] (4) After the reverse side is polished and other conditions remain unchanged, the polishing pressure value is set to 20 psi, and the flow rate of the polishing liquid is 10 ml / min.
[0026] (5) Ultrasonic cleaning in a cleaning solution with a concentration of 20% and a temperature of 100°C for 20 minutes, fully flushed, then corroded in 80°C hot acid for 3 minutes, and soaked in cold alkali (ammonia) for 2 minutes.
[0027] Experimenta...
PUM
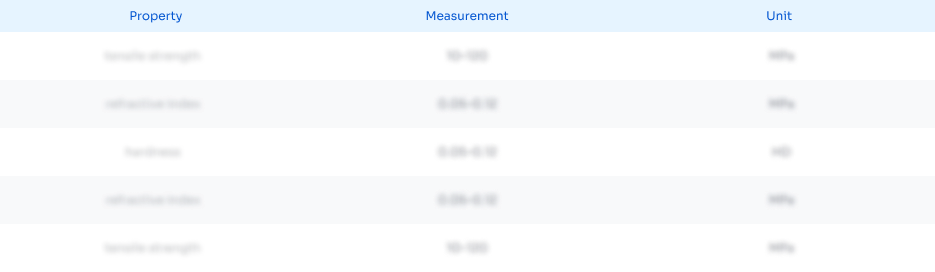
Abstract
Description
Claims
Application Information

- R&D
- Intellectual Property
- Life Sciences
- Materials
- Tech Scout
- Unparalleled Data Quality
- Higher Quality Content
- 60% Fewer Hallucinations
Browse by: Latest US Patents, China's latest patents, Technical Efficacy Thesaurus, Application Domain, Technology Topic, Popular Technical Reports.
© 2025 PatSnap. All rights reserved.Legal|Privacy policy|Modern Slavery Act Transparency Statement|Sitemap|About US| Contact US: help@patsnap.com