Biomass fuel boiler
A biomass fuel and boiler technology, applied in the boiler field, can solve the problems of reduced heat exchange efficiency, long boiler start-up time, large water content, etc., to ensure heat exchange efficiency and silo safety, shorten start-up time, and long service life Effect
- Summary
- Abstract
- Description
- Claims
- Application Information
AI Technical Summary
Problems solved by technology
Method used
Image
Examples
Embodiment 1
[0023] The biomass fuel boiler is suitable for yellow straw biomass with high tar content. Shaft flue 6, primary air chamber 7, secondary air supply device, water-cooled vibrating grate 8, economizer 9, air preheater 10, blower (not shown), etc., wherein the furnace 2, the first flue 4 and the second flue 5 are all provided with a water-cooled wall and a header; as shown in Figure 3, the primary air chamber is connected with the hot air passage of the air preheater through the air pipe; The secondary tuyeres in the furnace below the material pipe, and several secondary tuyeres arranged on the left and right sides of the furnace, (as shown in Figure 1 and Figure 4, the secondary tuyeres 20 are arranged in a staggered manner), all the secondary tuyeres are It is connected with the hot air passage of the air preheater, and there are adjusting baffles in each air outlet of the primary air chamber and all secondary air outlets, and the tail shaft flue is also connected with the dus...
Embodiment 2
[0026] This biomass fuel boiler is suitable for gray straw biomass with low tar content. As shown in Figure 2, the difference between it and Embodiment 1 is that the rear panel superheater 21 in front of the slag tube bundle 13 replaces the first one in the figure. A panel superheater 14 in the flue 4, because the tar content of the gray straw is low, it is not easy to coke even at high temperatures, and the pipes will not be corroded, thereby ensuring heat exchange efficiency.
PUM
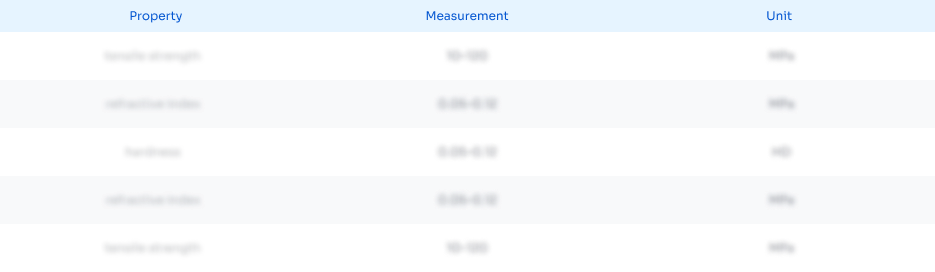
Abstract
Description
Claims
Application Information

- R&D Engineer
- R&D Manager
- IP Professional
- Industry Leading Data Capabilities
- Powerful AI technology
- Patent DNA Extraction
Browse by: Latest US Patents, China's latest patents, Technical Efficacy Thesaurus, Application Domain, Technology Topic, Popular Technical Reports.
© 2024 PatSnap. All rights reserved.Legal|Privacy policy|Modern Slavery Act Transparency Statement|Sitemap|About US| Contact US: help@patsnap.com