Method for producing spinning dyeing viscose fiber and spinning dyeing viscose fiber thereof
A technology of viscose fiber and production method, which is applied in the production of spinning dyed viscose fiber and the field of spinning dyed viscose fiber, which can solve the problem of unstable color of colored viscose fiber, the inability to control the oxidation-reduction process, and the inability to realize large-scale production and other problems, to achieve the effect of rich color varieties, good spinnability, and improved color fastness
- Summary
- Abstract
- Description
- Claims
- Application Information
AI Technical Summary
Problems solved by technology
Method used
Image
Examples
Embodiment 1
[0045] Example 1: acid environment oxidation
[0046] A. Preparation of color paste: According to the requirements of viscose fiber color, weigh a certain amount of one or several dyes according to the concentration ratio, mix and disperse them in desalted water, add alkaline solution, and then according to the reaction molar ratio, in Add reducing agent and oxidizing agent to the solution, and finally use desalinated water to make up the volume, then filter the solution into the storage tank, filter to remove particulate impurities, and make a color paste for later use;
[0047] Wherein, the adding amount of the reducing agent and the oxidizing agent is respectively 1-5 times and 0.5-2 times of the reaction mole number.
[0048] Dyes include: vat dyes, sulfur dyes, water-insoluble organic dyes
[0049] Alkaline solution can use NaOH aqueous solution.
[0050] Reaction molar ratio: determined according to the reaction formula of different dyes.
[0051] The reducing agent i...
Embodiment 2
[0073] Embodiment 2: alkaline environment oxidation
[0074] A. Preparation of color paste: According to the requirements of viscose fiber color, weigh a certain amount of one or several dyes according to the concentration ratio, mix and disperse them in desalted water, add alkaline solution, and then according to the reaction molar ratio, in Add reducing agent and oxidizing agent to the solution, and finally use desalinated water to make up the volume, then filter the solution into the storage tank, filter to remove particulate impurities, and make a color paste for later use;
[0075] Wherein, the adding amount of the reducing agent and the oxidizing agent is respectively 1-5 times and 0.5-2 times of the reaction mole number.
[0076] Dyes include: vat dyes, sulfur dyes, water-insoluble organic dyes.
[0077] Alkaline solution can use NaOH aqueous solution.
[0078] Reaction molar ratio: determined according to the reaction formula of different dyes.
[0079] The reducing...
Embodiment 3
[0102] Embodiment 3: embroidery thread production method
[0103] After the humidity-conditioning process in Example 1 and Example 2, the spun and dyed viscose fiber cakes are ternary, twisted, twisted or rolled into colored embroidery threads. Processes such as skeining, dyeing, opening, and barreling of colored silk are omitted.
PUM
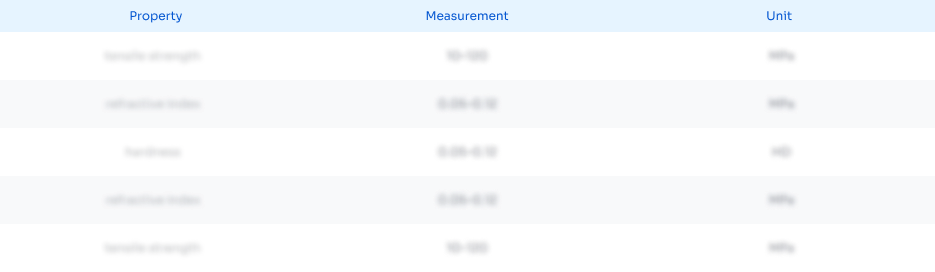
Abstract
Description
Claims
Application Information

- R&D
- Intellectual Property
- Life Sciences
- Materials
- Tech Scout
- Unparalleled Data Quality
- Higher Quality Content
- 60% Fewer Hallucinations
Browse by: Latest US Patents, China's latest patents, Technical Efficacy Thesaurus, Application Domain, Technology Topic, Popular Technical Reports.
© 2025 PatSnap. All rights reserved.Legal|Privacy policy|Modern Slavery Act Transparency Statement|Sitemap|About US| Contact US: help@patsnap.com