Process of producing bamboo chipboard
A manufacturing method and technology of large bamboo sheets, applied in the direction of manufacturing tools, flat products, pretreatment of molding materials, etc., to achieve the effect of reducing production cost, reducing bamboo raw material cost and production cost, and improving utilization rate
- Summary
- Abstract
- Description
- Claims
- Application Information
AI Technical Summary
Problems solved by technology
Method used
Image
Examples
Embodiment 1
[0046] Use more than 2-year-old dragon bamboo, cut the bamboo stalks into 70mm long bamboo tubes, slice the bamboo tubes into 0.5±0.1mm thick bamboo shavings along the longitudinal diameter (see figure 1 or figure 2 ). The bamboo shavings are placed in a drum dryer, dried to a moisture content of 7%, and sprayed with 10% melamine-modified urea-formaldehyde resin by a drum mixer. The large flakes after sizing were dried to a moisture content of 8%. According to the relationship between the density of dragon bamboo itself, the average density of dragon bamboo boards and the target performance, the target density is set at 0.763g / cm 3 And convert it into the paving quantity of glue-containing shavings per unit area, and lay them into a single-layer random structure slab according to the uncertain axis angle β of the shavings (such as Figure 7As shown), the slab is pre-pressed with a pre-pressing pressure of 1.5Mpa, the temperature of the hot-pressing plate is set to 140°C, t...
Embodiment 2
[0048] Repeat Example 1, with the following differences: select raw moso bamboo for more than 2 years, cut it into long and thin bamboo strips with a thickness of 0.6 ± 0.1mm along the longitudinal direction of the bamboo stalk with a cutting machine, and then cut it with a cutting machine Become 120mm long bamboo shavings. Spray sizing with phenolic resin at a ratio of 7%, and set the target density as 0.726g / cm according to the relationship between the density of moso bamboo itself, the average density of moso bamboo boards and the target performance 3 And converted into the pavement amount of glue-containing shavings per unit area, set the hot-pressing time to 12 minutes, and press to obtain a phenolic resin single-layer random structure bamboo large shaving slab with a length of 2440mm, a width of 1220mm, and a thickness of 10mm. It replaces wooden boards and is used as outdoor packaging box boards and I-beam webs with good results.
Embodiment 3
[0050] Repeat embodiment 1, have following difference: with more than 2 years raw hemp bamboo, bamboo stalk is cut into the bamboo tube of 150mm length, along the vertical diameter surface the bamboo tube is sliced into thick bamboo shavings of 0.7 ± 0.1mm. Spray sizing with 8% phenolic resin. According to the relationship between the density of hemp bamboo itself, the average density of hemp bamboo boards and the target performance, the target density is set to 0.836g / cm 3 And convert it into the pavement amount of rubber-containing shavings per unit area, and pave into a single-layer oriented structure slab (such as Figure 8 Shown), set the hot pressing time to be 13min, press to obtain 2440mm long, 1220mm wide, 10mm thick quality standard phenolic resin single layer oriented structure bamboo flake slabs. It replaces wooden boards and is used as outdoor packaging box boards and I-beam webs with good results.
PUM
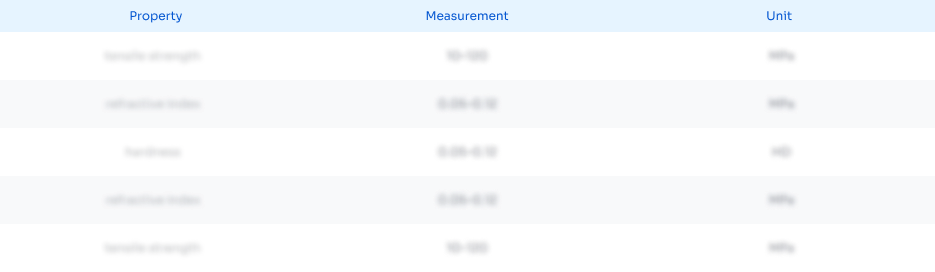
Abstract
Description
Claims
Application Information

- R&D
- Intellectual Property
- Life Sciences
- Materials
- Tech Scout
- Unparalleled Data Quality
- Higher Quality Content
- 60% Fewer Hallucinations
Browse by: Latest US Patents, China's latest patents, Technical Efficacy Thesaurus, Application Domain, Technology Topic, Popular Technical Reports.
© 2025 PatSnap. All rights reserved.Legal|Privacy policy|Modern Slavery Act Transparency Statement|Sitemap|About US| Contact US: help@patsnap.com