Method for reducing coal-firing boiler NOx discharge and its implementing device
A boiler and fuel technology, which is applied in the combustion method, burners for burning powder fuel, burners, etc., can solve the problems of ammonia penetration, incomplete reduction reaction, and increased NOx emission concentration.
- Summary
- Abstract
- Description
- Claims
- Application Information
AI Technical Summary
Problems solved by technology
Method used
Image
Examples
Embodiment Construction
[0023] The principle of the dual-stage re-reduction low-NOx pulverized coal burner of the present invention: the double-stage re-reduction low-NOx pulverized coal burner organizes multi-stage anoxic combustion of the main pulverized coal burner (excess air coefficient 0.9), effectively suppressing the formation of NOx in the main burner area , and then inject 10% graded fuel into the flame center downstream of the main burner, the graded fuel decomposes rapidly under the condition of high temperature and oxygen deficiency to generate a large amount of CH i group, CH i The radicals then reduce the NOx produced in the main burner area to N 2 , the CO produced by the anoxic combustion of graded fuels expands the reduction reaction temperature window of the SNCR method. Therefore, amino groups are injected into the cross-section with an average flame temperature of 1100°C for selective non-catalytic reduction of NOx, and then alkali metal salts are used to reduce the NOx. Process...
PUM
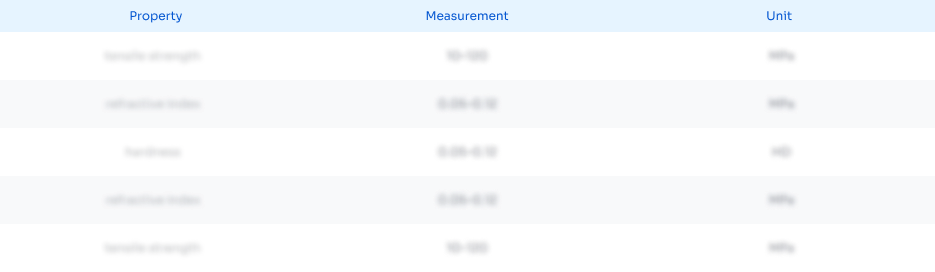
Abstract
Description
Claims
Application Information

- Generate Ideas
- Intellectual Property
- Life Sciences
- Materials
- Tech Scout
- Unparalleled Data Quality
- Higher Quality Content
- 60% Fewer Hallucinations
Browse by: Latest US Patents, China's latest patents, Technical Efficacy Thesaurus, Application Domain, Technology Topic, Popular Technical Reports.
© 2025 PatSnap. All rights reserved.Legal|Privacy policy|Modern Slavery Act Transparency Statement|Sitemap|About US| Contact US: help@patsnap.com