Stirring friction spot welding technology
A friction stir and spot welding technology, used in welding equipment, non-electric welding equipment, metal processing equipment, etc., can solve the problems of welding pressure into the pit, reducing the workload of processing, and many extrudates.
- Summary
- Abstract
- Description
- Claims
- Application Information
AI Technical Summary
Problems solved by technology
Method used
Image
Examples
Embodiment Construction
[0007] The invention designs the upper and lower shaft shoulders and the upper and lower stirring heads, and simultaneously rotates and pressurizes the upper and lower shaft shoulders and the stirring heads so that the welded parts form high quality solder joints.
[0008] Figure 1 is a schematic diagram of double-sided friction stir spot welding, 1 and 2 are parts to be welded, 3 is the upper shoulder, 4 is the upper stirring head, 5 is the lower shoulder, and 6 is the lower stirring head. The equipment parameters of the schematic diagram of the double-sided friction stir spot welding process shown in Figure 1 include: pressure F 1 , F 2 ;Rotation speed ω of shoulder 3, 5 1 ; Stirring head 4, 6 rotation speed ω 2 , and horizontal moving speed V; stirring head 4, 6 and shaft shoulder 3, 5 up and down moving stroke S; stirring head 4, 6 insertion depth h, insertion speed v 1 , the insertion residence time t, the withdrawal speed of the stirring head v 2 ; And parameters su...
PUM
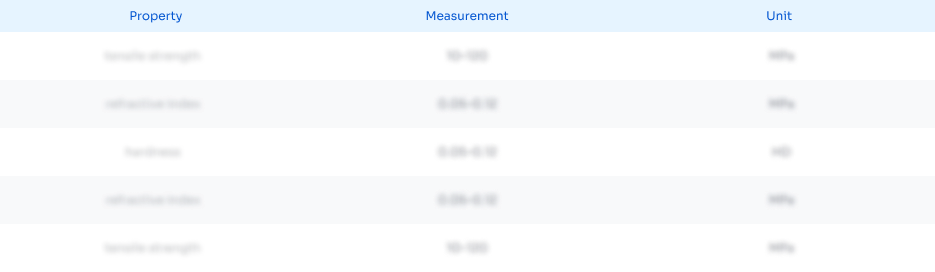
Abstract
Description
Claims
Application Information

- Generate Ideas
- Intellectual Property
- Life Sciences
- Materials
- Tech Scout
- Unparalleled Data Quality
- Higher Quality Content
- 60% Fewer Hallucinations
Browse by: Latest US Patents, China's latest patents, Technical Efficacy Thesaurus, Application Domain, Technology Topic, Popular Technical Reports.
© 2025 PatSnap. All rights reserved.Legal|Privacy policy|Modern Slavery Act Transparency Statement|Sitemap|About US| Contact US: help@patsnap.com