Preparation method of oil-filled insoluble sulphur
A sulfur and soluble technology, applied in the direction of sulfur preparation/purification, chemical instruments and methods, sulfur compounds, etc., can solve problems such as darkening of product color, high energy consumption of extraction agent recovery, and weak operation continuity, etc., to reduce Solvent loss, elimination of corrosion and waste water discharge, high volatility effect
- Summary
- Abstract
- Description
- Claims
- Application Information
AI Technical Summary
Problems solved by technology
Method used
Image
Examples
Embodiment 1
[0031] 1000g of sulfur with a content of 99% and 1g of composite stabilizer (KI0.5g, styrene 0.5g) were placed in a 3L reactor, and nitrogen gas was repeatedly charged 4 times to get rid of the air in the kettle. Start the program to heat up, and after the temperature in the kettle reaches 120°C and all the raw materials are melted, turn on the stirring device on the kettle. Continue to heat up to 300°C and keep the temperature for 25 minutes. Stop stirring after the reaction, open the valve at the bottom of the kettle, and the reaction raw materials directly flow into the quenching pool from the outlet of the valve. The quenching liquid is circulating water, and the on-site water temperature is 25°C. The product is a plastic mixture of soluble sulfur and insoluble sulfur, which is transferred to a blast dryer for curing treatment, controlled at a temperature of 80°C, and dried for 6 hours. The air-dried product that loses moisture is then transferred to a ball mill for crushi...
Embodiment 2
[0034] 1000g content is the sulfur of 99% and 3g composite stabilizer (wherein MgI0.6g, 2-methylstyrene 2.4g) is placed in 3L reactor, repeatedly fills with nitrogen 4 times to get rid of the air in the still. Start the program to heat up, and after the temperature in the kettle reaches 120°C and all the raw materials are melted, turn on the stirring device on the kettle. Continue to heat up to 240°C, and keep the temperature for 60 minutes. Stop stirring after the reaction, open the valve at the bottom of the kettle, and the reaction raw materials directly flow into the quenching pool from the outlet of the valve. The quenching liquid is circulating water, and the on-site water temperature is 15°C. The product is a plastic mixture of soluble sulfur and insoluble sulfur, which is transferred to a blast dryer for curing treatment, controlled at a temperature of 60°C, dried for 10 hours, and then moved to a ball mill to grind the product after air-drying and losing moisture, and...
experiment example 3
[0037] 1000g of sulfur with a content of 99% and 5g of composite stabilizer (KI0.36g, MgI0.36g, thiazole 4.28g) were placed in a 3L reactor, and nitrogen was repeatedly charged 4 times to get rid of the air in the kettle. Start the program to heat up, and after the temperature in the kettle reaches 120°C and all the raw materials are melted, turn on the stirring device on the kettle. Continue to heat up to 270°C, and keep the temperature for 40 minutes. Stop stirring after the reaction, open the valve at the bottom of the kettle, the reaction raw materials directly flow into the quench tank from the outlet of the valve, the quench liquid is circulating water, and the on-site water temperature is 100°C (adding ice cubes to the quench tank is used to reduce the water temperature). The product is a plastic mixture of soluble sulfur and insoluble sulfur, which is transferred to a blast dryer for curing treatment, controlled at a temperature of 50°C, and dried for 15 hours. Sievin...
PUM
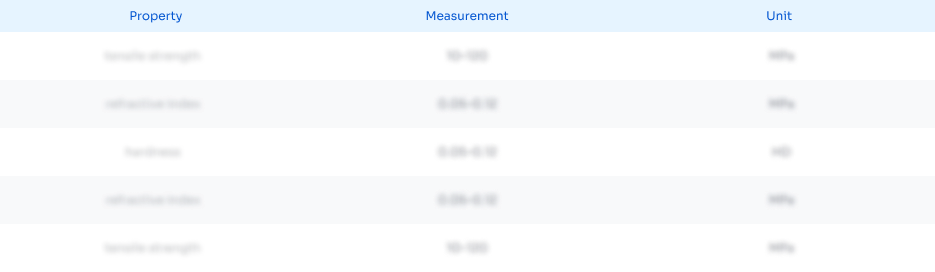
Abstract
Description
Claims
Application Information

- R&D
- Intellectual Property
- Life Sciences
- Materials
- Tech Scout
- Unparalleled Data Quality
- Higher Quality Content
- 60% Fewer Hallucinations
Browse by: Latest US Patents, China's latest patents, Technical Efficacy Thesaurus, Application Domain, Technology Topic, Popular Technical Reports.
© 2025 PatSnap. All rights reserved.Legal|Privacy policy|Modern Slavery Act Transparency Statement|Sitemap|About US| Contact US: help@patsnap.com